Lutowanie jest wyjątkowym etapem całego procesu produkcji w branży elektronicznej. To zespół czynności, które łączą trudy projektowania, obliczeń, symulacji, prób i testów, a także wszelkie starania organizacyjno-zaopatrzeniowe i przekształcają je w rzeczywisty obwód elektroniczny, który jest w stanie realizować określone zadania.
Taki opis celowo podkreśla ważność tego etapu. Gdyby okazało się, że przez niewłaściwie dobrane parametry lutowania, wyprowadzenia któregoś elementu zostałyby niedolutowane, to urządzenie nie działałoby prawidłowo. Podobnie wygląda sytuacja w przypadku lutowania, jako etapu naprawy. Brak odpowiedniego sprzętu doprowadzi to sytuacji, w której uszkodzony element zostanie zastąpiony nowym, uszkodzonym w trakcie montażu elementem, a dodatkowo mogą ucierpieć inne elementy czy nawet płytka PCB.
Zanim zaczniemy omawianie technik i sprzętu do montażu, dokonamy przeglądu najczęściej używanych obudów elementów SMD. Praktyczna znajomość rodzajów i stosowanych oznaczeń pozwala wyobrazić sobie wygląd elementu i ocenić wymagania montażowe.
Mniejsze wymiary, więcej korzyści
Korzyści płynących z zastosowania montażu powierzchniowego SMD (Surface-Mounted Devices) jest wiele. W porównaniu z tradycyjnym montażem przewlekanym THT (Through Hole Technology) układy powierzchniowe charakteryzują się znacznie większą gęstością upakowania, wyższą maksymalną częstotliwością pracy, a także lepszą odpornością na wibracje. Montaż powierzchniowy w całości poddaje się automatyzacji, co oprócz obniżenia kosztów produkcji korzystnie wpływa również na niezawodność finalnego produktu. Ostatecznie, zdecydowana większość nowoczesnych układów i elementów jest dostępna wyłącznie w obudowach do montażu powierzchniowego.
Rezystory i małe elementy bierne
Obudowy elementów biernych, ale także niektóre diody, bezpieczniki, termistory, ferryty oraz cała masa innych zostały sklasyfikowane zgodnie z wykazem pokazanym na rysunku 1.
Są to obudowy typu chip ich rozmiary są zgodne ze standardami branżowymi, takimi jak specyfikacje JEDEC. Oprócz wymiarów mają dokładnie określone opakowania w postaci papierowych lub plastikowych taśm przystosowanych do montażu automatycznego.
Nie są to wszystkie dostępne warianty – wybrane zostały te, które są praktycznie stosowane. Wymiary są zakodowane w ich nazwie, dokładne zestawienie pokazuje tabela 1.
Przykładowa obudowa 1206 ma wymiary 120×60 milsów (1 mils to 1/1000 cala, czyli 25,4 µm). Przeliczając na milimetry i zaokrąglając uzyskujemy więc 3,1×1,5 mm. Przyjęło się stosować calowe jednostki długości, ale można spotkać również oznaczenia w systemie metrycznym. Czasami powoduje to nieporozumienia, w szczególności przy obudowach 0402 i 0603, ponieważ takie oznaczenia występują zarówno w systemie calowym, jak i metrycznym. Dlatego przy stosowaniu systemu metrycznego zaleca się dodanie litery M, np. M0402, M0603.
Należy pamiętać, że wraz z wymiarami elementów zmienia się ich dopuszczalna moc strat – wartości tego parametru również zostały zawarte w tabeli 1.
Warto zwrócić uwagę na ten fakt zwłaszcza wtedy, gdy decydujemy się na zastosowanie najmniejszych dostępnych elementów. Sytuację doskonale podkreśla fotografia 1.
Kondensatory
Aluminiowe kondensatory elektrolityczne SMD mają konstrukcję zbliżoną do swoich przewlekanych odpowiedników. Walcowy, aluminiowy kubek uzupełniono kwadratową, plastikową podstawą z płasko wyprofilowanymi wyprowadzeniami (rysunek 2).
Normalizacji podlega jedynie średnica kubka: 3; 4; 5; 6,3; 8; 10; 12,5; 16; 18 mm, natomiast wymiary podstawy, nieco większe od średnicy walca, różnią się w zależności od producenta. Na szczęście różnice te są niewielkie, co umożliwia stosowanie jednolitych wzorów pól lutowniczych i zamienne stosowanie na jednej płytce kondensatorów różnych firm.
W tabeli 2 zestawiono orientacyjne wymiary maksymalne, wybrane z kilku katalogów. Całkowity bałagan panuje za to w firmowych oznaczeniach obudów. Każdy producent używa własnego systemu, a na domiar złego oznaczenia te potrafią być między sobą sprzeczne. Dlatego też zamiast nazw symbolicznych, w celu jednoznacznej identyfikacji rozmiaru obudowy najwygodniej jest używać kombinacji nominalnej średnicy i wysokości kubka, np. 6,3×8. Przy okazji przypomnijmy, że biegunowość wyprowadzeń kondensatorów elektrolitycznych może być oznaczona na dwa sposoby: drukowanym paskiem na wierzchu obudowy (elektroda ujemna) oraz ścięciem narożników podstawy (elektroda dodatnia).
Elektrolityczne kondensatory tantalowe SMD mają zupełnie inną konstrukcję – rysunek 3). Mają formę „cegiełkową” zbliżoną do obudów chip, jednak o innym kształcie elektrod i wykonaną w osobnym szeregu wymiarowym. Ich podstawowe oznaczenie składa się również z dwóch liczb, czyli łącznie 4 cyfr, określających wymiary poziome – jednak tym razem wyrażonych w dziesiątych częściach milimetra (0,1 mm). Zamiennie stosuje się również oznaczenia jednoliterowe: A...E, V – (tabela 3).
Przypomnijmy, że w przeciwieństwie do kondensatorów aluminiowych, kreska nadrukowana na obudowie kondensatora tantalowego oznacza elektrodę dodatnią (+).
Układy scalone
Dużo większe zróżnicowanie dotyczy elementów półprzewodnikowych, a zwłaszcza układów scalonych. Zmiana dominującej techniki montażu nie przeszkodziła jednak utrwaleniu istniejącego podziału na trzy zasadnicze klasy. Pierwsza to obudowy dwurzędowe wywodzące się w prostej linii z rodziny DIP, a noszące w technologii SMT nazwy zawierające wspólny rdzeń SO (Small Outline). Początkowo były to obudowy SOIC (SO–xx) a następnie stopniowo zagęszczane i spłaszczane obudowy z rodziny SOP (Small Outline Package) oznaczane m.in. PSOP (Plastic...), SSOP (Shrink...), TSOP (Thin...), VSOP (Very Thin…).
Na fotografii 2 zostały porównane przykładowe płytki, adaptery przeznaczone dla układów w obudowach SOP i SSOP.
Drugą klasą obudów są płaskie obudowy prostokątne (najczęściej kwadratowe) z wyprowadzeniami rozmieszczonymi na czterech bokach i zawierające w oznaczeniach literę Q (Quad). Wśród nich najliczniej reprezentowane są obudowy z rodziny QFP (Quad Flat Pack) takie jak np. PQFP, TQFP, VQFP wyposażone w płaskie nóżki, wystające poza obrys korpusu i uformowane w kształcie przypominającym skrzydło mewy (stąd też pochodzi ich nazwa gull–wings). Kilka typów obudów tego typu pokazano na rysunku 4.
Obecnie dominującymi typami obudów są wersje beznóżkowe, w których wyprowadzenia są zatopione w korpusie, widoczne tylko na dolnych krawędziach i na spodzie. Reprezentowane są m.in. przez rodzinę QFN (Quad Flat Noleads) – rysunek 5.
Warto wspomnieć, że te obudowy często są wyposażone w duże metaliczne pole na spodzie (lub kila mniejszych pól), które służą do odprowadzania ciepła z układu – jest to tzw. thermal pad. Jako ciekawostkę warto pokazać np. obudowę układu MAX20735 (rysunek 6), który jest kompletnym scalonym stabilizatorem impulsowym o prądzie wyjściowym do 40 A.
Trzecią kategorią obudów są te z matrycowym układem wyprowadzeń (Grid Array) reprezentowane w dziedzinie SMD przez bardzo liczną rodzinę BGA (Ball Grid Array). Wspólną cechą łączącą obudowy BGA jest wykonanie wyprowadzeń w postaci małych okrągłych padów rozmieszczonych na spodzie obudowy. Często zawierają przylutowane kulki stopu lutowniczego, które ulegają przetopieniu podczas montażu (fotografia 3).
Typowy układ BGA składa się z niewielkiej struktury krzemowej (silicon die) umieszczonej na znacznie większej płytce PCB (carrier). Pomiędzy nimi znajdują się połączenia elektryczne w postaci cienkich drucików rozprowadzające wyprowadzenia struktury na odpowiednie pady na płytce. Jest to konstrukcja charakterystyczna dla dużych wersji układów. Natomiast coraz częściej dostępne są niewielkie układy o podobnej konstrukcji w obudowach oznaczanych jako CSP oraz WLCSP. Pierwotnie oznaczenie CSP było akronimem oznaczającym obudowę wielkości chipa (Chip-Scale Package). W praktyce tylko kilka obudów ma rzeczywistą wielkość struktury krzemowej, zwykle dodawana jest cienka przekładka zawierająca połączenia, pady i soldermaskę, dlatego znaczenie akronimu zostało zmodyfikowane. Został przyjęty standard, który określa, że powierzchnia obudowy może mieć powierzchnię maksymalnie 1,2 razy większą niż struktura krzemowa, aby zakwalifikowała się jako CSP. Dopiero w przypadku, gdy wyprowadzenia układu – pady, są umieszczone bezpośrednio na strukturze krzemowej, to obudowa jest bardzo zbliżona do rozmiaru struktury – wafla krzemowego. Stąd wywodzi się naza WLCSP – Wafer-Level Ship-Scale Package. Uproszczone porównanie trzech omówionych typów obudów zostało pokazane na rysunku 7, od strony montażowej, wszystkie traktujemy jako układy BGA.
Raster
Przejście na montaż powierzchniowy pozwoliło na znaczne zagęszczenie końcówek. Początkowo dwukrotne tzn. do 1,27 mm (50 milsów), stopniowo zmniejszanego, w miarę rozwoju technologii wytwarzania płytek drukowanych i precyzji montażu. Obecnie w scalonych układach SMD można spotkać następujące, wartości rastra: 1,27 mm (0,05”); 1,25 mm; 1,00 mm; 0,95 mm; 0,80 mm; 0,75 mm; 0,65 mm; 0,635 mm (0,025”); 0,55 mm; 0,50 mm; 0,40 mm. To spora ilość. Na szczęście, tych powszechnie stosowanych jest tylko kilka – wyróżniono je pogrubionym drukiem. Stopień upakowania wyprowadzeń znajduje swoje odbicie w nazwach obudów zawierających przymiotniki Shrink lub Fine.
Montaż układów o gęstych rastrach nie toleruje żadnych błędów. Krótkie i gęsto rozmieszczone wyprowadzenia muszą z dużą precyzją trafiać na właściwe pola. Próby korekty zwykle kończą się uszkodzeniem elementów lub płytki PCB.
Montaż produkcyjny
Marzeniem każdego projektanta jest możliwość swobodnego korzystania z jak najszerszej gamy elementów, niezależnie od sposobu ich montażu. Profesjonalne linie montażowe zapewniają takie możliwości, dlatego przeanalizujemy stosowane tam technologie.
Każda technika lutowania miękkiego, a z takim mamy do czynienia w naszym przypadku, polega na kilku podstawowych czynnościach: podgrzaniu złącza do wymaganej temperatury, dostarczeniu topnika usuwającego zanieczyszczenia i podaniu stopu lutowniczego tworzącego właściwą spoinę. W montażu jednostkowym stosowane jest kontaktowe lutowanie metodą „punkt po punkcie” tzn. gorącym grotem lutownicy i spoiwem z topnikiem. W przypadku produkcji obwodów drukowanych z elementami przewlekanymi stosowane jest lutowanie na fali (wave soldering), polegające na obsadzeniu górnej strony płytki drukowanej wszystkimi elementami a następnie przeciągnięciu jej dolnej powierzchni przez grzbiet fali utworzonej ze strumienia ciekłego stopu lutowniczego (fotografia 4).
Stopiony metal nagrzewa punkty lutownicze i osadza się na nich tworząc połączenia. Lutowanie na fali zdecydowanie przyspiesza montaż, jednak w odróżnieniu od tradycyjnego lutowania punktowego naraża laminat i podzespoły na znacznie większe obciążenia termiczne. Przystosowanie metody lutowania na fali do montażu powierzchniowego SMT (Surface Mount Technology) wymagało dodatkowego, czasochłonnego zabiegu, który polega na wstępnym przyklejaniu podzespołów SMD do laminatu. To przyczyniło się do rozwinięcia techniki lutowania rozpływowego (reflow soldering).
Szablony SMT
Najpierw nanosi się na pola lutownicze cienką warstwę lutowia wraz z topnikiem w postaci lepkiej pasty (fotografia 5).
Stosuje się do tego szablony wykonane z metalu w formie sita (fotografia 6).
Po przyłożeniu szablonu do płytki drukowanej, otwory sita trafiają dokładnie w takich miejscach, że odsłaniają wyłącznie punkty lutownicze elementów SMD. Od górnej strony nakłada się pastę lutowniczą i zgarnia jej nadmiar raklą. Po zdjęciu szablonu na płytce pozostaje cienka warstwa pasty lutowniczej (o grubości równej grubości szablonu) wyłącznie w miejscach otworów sita, czyli na padach lutowniczych. Taka jest ogólna zasada działania wszystkich sitodrukarek do nakładania pasty lutowniczej – zarówno ręcznych jak i w pełni automatycznych. Różnica między nimi polega na skali automatyzacji – albo wszystkie czynności są wykonywane ręcznie, albo w sposób zautomatyzowany.
Układanie elementów
Następnym etapem jest umieszczenie na płytce elementów. Służą do tego maszyny typu pick & place (fotografia 7).
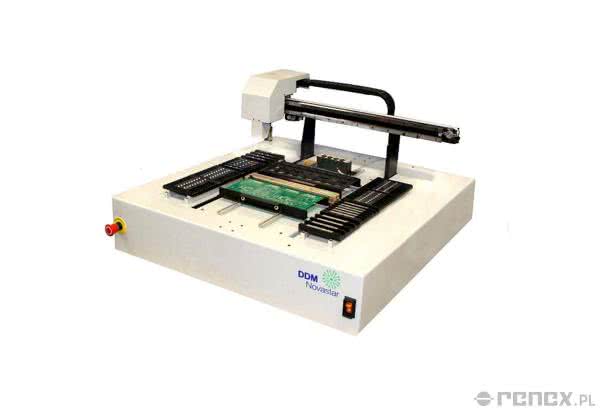
Głównym elementem układającym są głowice wyposażone w ssawki. Zasobnikami w których zgromadzone są komponenty są podajniki (feeders). Głowica ma swobodę ruchów w płaszczyźnie poziomej – podjeżdża nad podajnik, zniża ssawkę do komponentu, następnie włącza podciśnienie w i w ten sposób podnosi element. Wiele głowic jest wyposażonych w specjalne szczęki wyrównujące położenie komponentu. Następnie komponent jest kładziony, wyłączane jest podciśnienie w ssawce, żeby pozostawić komponent na swoim miejscu, a głowica odjeżdża po następny komponent. Większość nowoczesnych automatów ma kilka głowic pracujących równocześnie i dzięki temu proces układania elementów przebiega kilkakrotnie szybciej.
Głowice dodatkowo mogą być wyposażone w układ wizyjny. Komponent przed położeniem na płytce jest transportowany nad kamerę a wbudowany komputer analizuje obraz i na tej podstawie wykonuje korekcję położenia komponentu. Dzięki temu elementy są ułożone na płytce bardzo precyzyjnie.
Lutowanie rozpływowe
Płytki z elementami SMD ułożonymi na paście lutowniczej trafiają do pieca lutowniczego (fotografia 8), gdzie przebywają określony czas w kolejnych strefach.
W każdej z nich jest utrzymywana ściśle określona temperatura, pozwala to na uzyskanie odpowiedniego profilu temperaturowego. Strefy początkowe mają za zadanie podnieść temperaturę płytki i komponentów do wartości bliskiej temperatury topnienia i ustabilizować tą temperaturę – jest to ważne, ponieważ komponenty różnią się rozmiarem, masą i pokryciem i jedne z nich szybciej się nagrzewają, inne wolniej, dlatego konieczne jest dość długie rozgrzewanie komponentów tak, żeby wszystkie osiągnęły docelową temperaturę. Następnie płytka trafia do strefy rozpływu. Tutaj temperatura przekracza temperaturę topnienia pasty i następuje jej roztopienie. W kolejnych strefach następuje zastyganie lutowia i stopniowe schładzanie płytki. Do nagrzewania obwodu drukowanego w piecu tunelowym stosuje się promienniki podczerwieni lub wymuszoną konwekcję gorącego powietrza.
Prototypowanie i serwisowanie
Produkcja na niewielką skalę często uniemożliwia zlecenie montażu u zewnętrznego usługodawcy lub niewspółmiernie podnosi koszty takiego zlecenia. Producenci sprzętu od dawna dostrzegali zapotrzebowanie w takim obszarze produkcji i dlatego zostały opracowane urządzenia stosujące techniki podobne do produkcyjnych sprowadzone do skali montażu jednostkowego. Począwszy od lutownicy grzałkowej wyposażonej w grot typu minifala symulujący w mikroskali falę stopionego lutowia, przez stacje lutownicze z nadmuchem gorącego powietrza stosowane do montażu i demontażu elementów o niewielkich gabarytach, aż do stacji z promiennikami IR przeznaczonymi do elementów BGA i małymi piecami do lutowania w technice rozpływowej.
Największą trudność w montażu podzespołów SMD stanowią ich miniaturowe gabaryty i zwarta konstrukcja. To utrudnia dokładne pozycjonowanie tych podzespołów oraz ocenę jakości wykonanego montażu i wyszukiwanie uszkodzeń – zwarć czy niedolutowań. Mając na uwadze takie argumenty, omawianie niezbędnych narzędzi rozpoczniemy od tych, które wspomagają cały ten proces.
Narzędzia optyczne
Do wykonania większości operacji związanych z lutowaniem i demontażem SMD zwykle wystarcza podświetlana lupa warsztatowa zamontowania na wysięgniku lub lupa nagłowna. Pozycjonowanie układów o gęstym rastrze np. 0,5 mm oraz kontrola jakości wykonanych lutowań wymaga już powiększeń rzędu 10...15 razy. Niestety jednosoczewkowe lupy o krótkich ogniskowych wprowadzają duże zniekształcenia co poważnie uprzykrza posługiwanie się nimi. Swobodę pracy wynikającą z dobrej jakość obrazu w całym polu roboczym zapewnia dopiero mikroskop stereoskopowy na statywie o długim ramieniu i powiększeniu regulowanym w zakresie od kilku do kilkudziesięciu razy, np. taki jak pokazany na fotografii 9. Natomiast z dużą nieufnością należy podchodzić do mikroskopów cyfrowych – z wyświetlaczem LCD lub wyposażonych w interfejs USB. Prezentacje reklamowe takich urządzeń często nie mają odzwierciedlenia w faktycznej jakości obrazu, który możemy za ich pomocą uzyskać.
Nie jest to regułą, ale należy mieć to na uwadze decydując się na urządzenie tego typu.
Warto wiedzieć, że możliwa jest także inspekcja optyczna elementów w obudowach BGA. Podstawowym zadaniem takiego systemu jest tworzenie obrazu ze szczeliny o wysokości nieprzekraczającej 500 µm. W tym celu głowica analizująca potrzebuje źródła światła i specjalnych elementów optycznych zakrzywiających światło, które składają się zazwyczaj z pryzmatu lub lustra połączonego z zakończeniem głowicy układu optycznego. Wygląd i działanie takiego urządzenia pokazuje fotografia 10.
Uzyskiwany obraz może być trudny do analizy i z pewnością wymaga doświadczenia. Jeszcze bardziej zaawansowaną technologią, która daje większe możliwości jest obrazowanie z użyciem promieniowania rentgenowskiego – efekty zostały pokazane na fotografii 11.
Stacja lutownicza
Stacje lutownicze budzą największe emocje wśród osób zainteresowanych techniką SMT. Klasyczna stacja z grzałką i regulacją temperatury jest obowiązkowym i niezastąpionym narzędziem, jednak spełni swoje zadanie tylko wtedy, gdy będzie wyposażona w odpowiedni grot. Skoro chcemy przymierzyć się do precyzyjnych elementów to w naturalnym odruchu wybierzemy ostrą końcówkę o rozmiarach porównywalnych z wymiarami złącz, czyli ok. 0,6...1 mm. Najważniejsze zadanie grota polega na skutecznym przekazywaniu ciepła. Zatem jego kształt powinien zapewnić możliwie dobre przyleganie do płytki i lutowanego elementu a tym samym małą rezystancję termiczną styku i szybkie nagrzewanie pola operacyjnego. Niedostateczne oddawanie ciepła skłania do nadmiernego forsowania temperatury lutownicy (istotnie powyżej 260...280°C niezbędnych do skutecznego wygrzania złącza) a w konsekwencji zwiększa ryzyko przegrzania płytki i elementów oraz przyspiesza utlenianie lutowia na grocie.
Większość stacji lutowniczych posiada w standardowym wyposażeniu jedynie groty z zakończeniem w kształcie zaokrąglonego stożka. Jednak takie groty mają bardzo małą powierzchnię styku, co znacznie zawęża zakres ich zastosowań. Zaskakująco dobrym rozwiązaniem jest wybranie grota o lekko spłaszczonej końcówce (w kształcie wąskiego śrubokręta) lub stożka ale z ukośnym ścięciem wierzchołka. Można nim montować drobne elementy (R, C, D, T) oraz układy scalone o niewielkiej liczbie wyprowadzeń i luźnym rastrze, a więc przede wszystkim SOIC czy PLCC. Zapewne nie da się uniknąć przy tym powstania kilku mostków, a już na pewno dużego zwarcia ostatnich wyprowadzeń (fotografia 12). Za sprawą szerokich separacji między polami lutowniczymi z łatwością usuniemy powstające zwarcia używając dobrego topnika lub dodatkowo miedzianej plecionki do usuwania nadmiaru cyny (fotografia 13).
W tym miejscu warto wspomnieć o pewnej niewłaściwej praktyce w posługiwaniu się plecionką. Po pierwsze, przez samym użyciem należy nasączyć topnikiem fragment, którym się posłużymy. Po drugie, nie należy usuwać spoiwa nadmiernie – plecionka bardzo skutecznie je „wciąga”. Wyprowadzenia intensywnie oczyszczone przy pomocy plecionki mogą mieć tak niewielką ilość spoiwa, że połączenie zostanie przerwane przy pierwszym niewielkim naprężeniu.
W przypadku elementów o gęstym rastrze, takim jak 0,65 mm, niezbędny jest grot typu minifala. Na jego końcu znajduje się wyżłobienie gromadzące zapas stopu wystarczający do zalutowania całego rzędu wyprowadzeń układu w obudowie typu QFP (fotografia 14). Minifalą operuje się czysto i bardzo wygodnie, a wyprowadzenia są dobrze nagrzewane i zwilżane przez lutowie penetrujące głęboko pod całe stopy wyprowadzeń. Możliwe są dwa sposoby prowadzenia – od góry po nóżkach lub po samych polach lutowniczych, na styk do wyprowadzeń układu. Każdy musi eksperymentalnie dojść do optymalnego ułożenia. Przed samym montażem na wyprowadzenia układu należy koniecznie nałożyć topnik żelowy a wgłębienie grota wypełnić na płasko świeżym lutowiem. Dobrze wykonana operacja minifalą powinna się udać za pierwszym razem, bez pozostawienia zwarć. Tym samym sposobem przylutujemy układy w obudowach typu QFN, jeśli pandy na płytce PCB wystają poza obrys obudowy układu – fotografia 15.
Lutownica grzałkowa z odpowiednim grotem umożliwi przylutowanie większości dostępnych elementów przeznaczonych do montażu powierzchniowego, a jednocześnie praktycznie nie nadaje się do ich wylutowywania. Można stosować różne techniki zalewania wyprowadzeń cyną lub używać specyficznych – szerokich lub rozdwojonych grotów, ułatwiających demontaż niektórych elementów, ale są to metody, które sprzyjają uszkadzaniu mechanicznemu lub termicznemu wrażliwych komponentów. Klasycznym przykładem są ukruszone wyprowadzenia rezystorów i kondensatorów SMD oraz przegrzane diody LED SMD. Jedynym rozwiązaniem, które rzeczywiście zasługuje na uwagę i pozwala na profesjonalny demontaż niektórych elementów SMD jest tzw. lutownica pęsetowa (desoldering tweezers), taka jak pokazana na fotografii 16.
Może być skonstruowana jako specjalna podwójna kolba do stacji lutowniczej lub jako samodzielne narzędzie. Składa się z dwóch grzałek i grotów, które jednocześnie rozgrzewają przeciwległe strony elementu, przy czym może to być więcej niż jedno wyprowadzenie na każdej ze stron.
Stacja lutownicza typu Hot Air
W miarę zwiększania rozmiarów obudów i liczby wyprowadzeń nagrzewanie kontaktowe staje się niemożliwe. Również w przypadku elementów miniaturowych oraz takich z wyprowadzeniami umieszczonymi pod układem – jest to niewykonalne. Najprostszym narzędziem, które można zastosować w takich przypadkach jest stacja lutownicza wyposażona w dyszę, która generujące strumień gorącego powietrza – tzw. Hot Air (fotografia 17).
Montaż i demontaż elementów elektronicznych za pomocą takiej stacji jest względnie prosty, chociaż dobre wyniki uzyskuje się dopiero po osiągnięciu wprawy. Prace należy rozpocząć od spokojnego podgrzania układu i jego okolic do ok. 110...130°C. Po osiągnięciu tego etapu można podnieść temperaturę strumienia powietrza do ok. 300°C, ale konkretna wartość powinna wynikać z własnej praktyki na danym egzemplarzu stacji. Kierując strumień gorącego powietrza bezpośrednio na element, a w przypadku układu scalonego – na jego wyprowadzenia, doprowadzamy do stopienia lutowia. Standardowa, okrągła dysza o średnicy 4...6 mm wystarcza do operowania strumieniem powietrza na tyle precyzyjnie, żeby rozlutować układ nie uszkadzając płytki w jego sąsiedztwie. Jednak im większa obudowa tym silniejsze stygnięcie wyprowadzeń między kolejnymi przejściami dyszy, a tym samym dłuższy całkowity czas nagrzewania. Rozwiązaniem może być wyposażenie nagrzewnicy w dysze kształtowe o rozmiarach dopasowanych do konkretnego typu obudowy i kierujące strumień gorącego powietrza wyłącznie na rzędy nóżek (fotografia 18). Niestety dysze kształtowe oprócz wielu zalet mają jedną istotną wadę – cenę.
Stacja lutownicza typu Rework Station
Stacje lutownicze Hot Air umożliwiają wykonanie wielu, nawet średnio skomplikowanych, prac na płytkach z elementami SMD. Jednak z pewnych względów wymagają sporego doświadczenia. Po pierwsze, nie są wyposażone w systemy kontroli temperatury obiektu i nie pozwalają na precyzyjne realizowanie profilu temperaturowego.
Po drugie, strumień gorącego powietrza z dyszy lutownicy „rozpływa się” dookoła podgrzewanego elementu i może np. stopić plastikowe elementy złącz czy przycisków, oraz może „zdmuchnąć” małe elementy SMD.
Do profesjonalnego i bezpiecznego lutowania, nawet dużych elementów BGA służą tzw. BGA Rework Station (fotografia 19). Ich konstrukcja jest dość rozbudowana. Głównym źródłem ciepła jest promiennik podczerwieni zrealizowany przy pomocy grzałki kwarcowej lub ceramicznej, emitujący promienie podczerwone, które nagrzewają obiekt. Dzięki temu można precyzyjnie ustawić obszar roboczy i nie powstają strumienie gorącego powietrza zagrażające wrażliwym komponentom. Na spodzie obszaru roboczego stacji znajduje się tzw. Preheater czyli grzałka powierzchniowa, która wstępnie podgrzewa całą lutowaną płytkę. Proces lutowania jest objęty kontrolą temperatury dzięki czujnikowi w postaci termopary, umieszczanemu tuż przy lutowanym układzie i możliwe jest ustawienie charakterystyki czasowo temperaturowej. Oprócz tego znajdują się specjalne uchwyty do płytki PCB, ssawka podciśnieniowa do bezpiecznego podnoszenia elementów, system oświetlenia, a w najlepszych modelach, także kamera z odpowiednią optyką i ekranem. Urządzenia tego typu są dosyć kosztowne, ale umożliwiają wykonywanie profesjonalnych zabiegów lutowania oraz wylutowywania i dzięki temu przyczynią się do szybkiego zwrotu zainwestowanego kapitału.
Piece do lutowania
Stanowisko z urządzeniem typu Rework Station nie jest do końca uzasadnione w przypadku, gdy głównym obszarem działalności będzie montaż produkcyjny. W przypadku niewielkich serii produkcyjnych i prototypowych optymalnym rozwiązaniem będzie mały piec lutowniczy, taki jak pokazany na fotografii 20.
Wzrost temperatury lutowania związany z wprowadzeniem lutowia bezołowiowego spowodował, że różnica pomiędzy temperaturą graniczną, powyżej której może nastąpić zniszczenie komponentów, a temperaturą lutowania znacznie się zmniejszył. Zatem kontrolowanie temperatury procesu lutowania musi być bardzo precyzyjne. Nie mniej ważne jest uzyskanie równomiernego rozłożenia temperatury na całej powierzchni płytki w celu uniknięcia naprężeń. Wszystko to jest możliwe do uzyskania tylko w piecach lutowniczych zawierających system grzałek. Zachowanie prawidłowego profilu temperaturowego daje pewność, że pasta lutownicza wytworzy prawidłowe połączenia lutowane, a elementy nie zostaną uszkodzone termicznie.
Profil temperaturowy
Termin ten został wymieniony już kilka razy, dlatego należy go dokładnie rozwinąć. Producenci past lutowniczych oferują szeroką gamę produktów różniących się m.in. składem, zawartością i wielkością ziaren stopu lutowniczego, aktywnością topnika i korozyjnością jego pozostałości, temperaturą odparowania rozpuszczalnika, a także lepkością i własnościami tiksotropowymi. Dla właściwego przebiegu procesu stopienia pasty lutowniczej musi być zachowana właściwa charakterystyka temperaturowo-czasowa, czyli tzw. profil temperaturowy.
Na rysunku 8 został pokazany przeciętny profil temperatury przez jaki musi przejść płytka w piecu do lutowania. Możemy go podzielić na 4 etapy.
- Nagrzewanie wstępne (preheat) – odbywa się z typowym nachyleniem ok. 1...2°C/s. trwa do osiągnięcia temperatury ok 100...120°C. Na tym etapie następuje odparowanie rozpuszczalnika zawartego w paście lutowniczej. Przekroczenie dopuszczalnego gradientu temperatury może być przyczyną powstania dwóch defektów tzn. kuleczkowania (balling) i zwarć pomiędzy wyprowadzeniami (bridging). Podczas wygrzewania pasty na jej powierzchni powstaje cienka wyschnięta błona. Gwałtowne nagrzewanie prowadzi do lokalnego wzrostu ciśnienia par rozpuszczalnika, przerwania warstwy powierzchniowej i rozpryśnięcia pasty wokół pola lutowniczego. Lutowie zawarte w rozproszonej paście przyjmuje, po przetopieniu, postać luźnych kulek, od których pochodzi nazwa defektu (fotografia 21).
- Zwilżanie lub oczyszczanie (soak) – w tej fazie zachodzą równolegle dwa procesy: aktywacja topnika i ujednolicenie rozkładu temperatur. Temperatura ok. 145°C stanowi próg aktywacji większości stosowanych topników. Oznacza to, że dopiero od tej chwili odbywa się chemiczne oczyszczanie powierzchni tworzących złącze jak i rozpuszczanie tlenków pokrywających ziarna stopu lutowniczego. Drugi etap trwa do momentu osiągnięcia temperatury ok. 190...210°C, aczkolwiek jego zalecany czas trwania zależy od metody nagrzewania. Niemniej czas ten powinien być wystarczająco długi, aby umożliwić usunięcie zanieczyszczeń, a zarazem nie przedłużany nadmiernie, gdyż powoduje przedwczesne wyczerpanie aktywnego zapasu topnika i wtórne utlenianie powierzchni odbijające się na jakości połączeń.
- Rozpływ (reflow) – zaczyna się z chwilą osiągnięcia temperatury topnienia stopu lutowniczego i polega na szybkim (z nachyleniem do 1...3°C/s) nagrzaniu do maksymalnej temperatury przekraczającej o 20...30°C temperaturę topienia lutowia, po czym równie szybkim schłodzeniu poniżej temperatury krzepnięcia stopu. W praktyce przyjmuje się odrobinę wyższą temperaturę maksymalną sięgającą 230…250°C. Faza rozpływu jest najbardziej krytyczna z punktu widzenia niezawodności montażu. Czas jej trwania wynosi 30...90 s (chociaż zaleca się <60 s). Od dołu ogranicza go m.in. czas potrzebny na penetrację spoiwa oraz gradienty temperatury wywołujące naprężenia termiczne prowadzące do uszkadzania elementów. Z drugiej strony podzespoły i laminat są poddawane działaniu ekstremalnie wysokiej temperatury, a przedłużanie procesu może prowadzić do ich uszkodzenia.
- Chłodzenie (cooling) – ostatnia faza powinna się odbywać względnie szybko ale nie przekraczając nachylenia 3…4°C/s, ze względu na naprężenia termiczne.
Jednym z bardziej widowiskowych defektów montażu SMT jest tzw. nagrobkowanie (tombstoning) polegające na stawianiu na sztorc drobnych podzespołów np. rezystorów (fotografia 22). Defekt ten powodują siły napięcia powierzchniowego występujące w stopionym lutowiu i z jakiegoś powodu działające niesymetrycznie na element.
Takim powodem może być np. słabe (na skutek złego działania topnika) lub opóźnione (w wyniku niejednorodnego rozkładu temperatury) zwilżanie jednego z dwóch pól lutowniczych, a jego przyczyn należy szukać w pierwszej kolejności w błędach popełnionych w drugiej fazie nagrzewania. Znajomość zjawisk zachodzących w czasie lutowania i powodowanych przez nie defektów powinny (jak sądzę) ułatwić zdobywanie tego doświadczenia.
Podsumowanie
Technologie lutowania obejmują wiele zagadnień nie omówionych w tym artykule. Wiele zależy od konkretnego typu laminatu, zastosowanych elementów, technologii lutowania, użytego spoiwa itd. Bardzo pomocne są dokumentacje szczegółowo opisujące wymagania dla tego procesu, udostępniane przez producentów komponentów i materiałów do lutowania. W przypadku montażu serii prototypowej można zdać się na doświadczenie i intuicję, ale przy końcowej produkcji bezwzględnie należy trzymać się tych wytycznych. Ewentualne koszty, które mogą wyniknąć z powodu wad poprodukcyjnych produktu, szybko przerosną koszty zlecenia montażu w profesjonalnej firmie.
Damian Sosnowski, EP
Bibliografia:
https://bit.ly/3i3l2x5
https://bit.ly/3y8IzSL
https://bit.ly/3eQqmBO
https://bit.ly/2Wjg7j7
https://bit.ly/3iPGVz5
https://bit.ly/3x5LgTV
https://bit.ly/3eSh5cq
https://bit.ly/3BDtDOK
https://bit.ly/3BGsxla
https://bit.ly/2V6dOPM
https://bit.ly/3zBox3Q
https://bit.ly/3kTrGYs
https://bit.ly/3i3kYgT