Mamy XXI wiek, lądownik Philae napędzany własnymi silnikami ląduje na komecie 67P/Czuriumow-Gierasimienko, zaś amerykańska agencja kosmiczna NASA ogłasza, że program załogowych lotów na Marsa rozpocznie się na dobre w okolicach 2025 roku! A na jakim etapie rozwoju jest rynek motoryzacyjny? Powiem Wam na jakim - jest w rękach ekonomistów i speców od marketingu!
Bo jak inaczej wytłumaczyć fakt, iż przy dzisiejszym stanie wiedzy, stopniu zaawansowania technologicznego obecnie produkowanych pojazdów (ale nawet tych sprzed 20 lat), które to już od dawna są wyposażane w różne komputery i sterowniki nadal elementem opcjonalnym (czyt. wymagającym dopłaty) jest dla wielu producentów z branży motoryzacyjnej tak zwany komputer pokładowy.
Sytuacja jest tym bardziej kuriozalna, iż wszystkie dane, które standardowo pokazuje urządzenie tego typu, dostępne są bez problemu z poziomu komunikacji ze sterownikiem silnika ECU, w jaki jest wyposażony każdy nowszy pojazd, więc ich ewentualne wyświetlenie to sprawa kilku linijek dodatkowego kodu.
Pikanterii sprawie dodaje fakt, że tak forsowana przez Unię Europejską polityka ekologiczna, która to w ostatnim czasie wymusiła na producentach pojazdów wyposażanie ich w czujniki niskiego ciśnienia powietrza w oponach, tłumacząc tego typu wymóg potrzebą zmniejszania emisji szkodliwych gazów do atmosfery (bo odpowiednio napompowana opona to mniejsze opory tarcia, co powoduje mniejsze spalanie paliwa) jakoś nie mogła "poradzić sobie" ze zmuszeniem tychże producentów do standardowego montażu komputerów pokładowych, które pokazując statystyki spalania jawnie wpisywałyby się we wszechobecną modę na rozwiązania ekologiczne.
No dobrze, polskim zwyczajem, trochę ponarzekałem, lecz czas brać się do "roboty". Wszak na naszych ulicach jeszcze jeździ sporo starszych pojazdów, których użytkownicy nawet nie mogli pomarzyć o takim luksusie. Ale czy to tak naprawdę luksus? Nie sądzę!
Wszak jest to urządzenie raczej nieskomplikowane, do którego działania potrzebne są w zasadzie tylko 2 sygnały: sygnał prędkości pojazdu dostępny zwyczajowo w złączu ISO każdego radioodbiornika oraz sygnał wtryskiwacza, który to możemy "pobrać" z dowolnego wtryskiwacza paliwa umieszczonego pod maską pojazdu (bez znaczenia czy pojazd jest zasilany benzyną czy olejem napędowym).
Pewnie zastanawiacie się czy nie przesadzam trochę w kwestii prostoty tego typu rozwiązań? Otóż nie, a opinię swoją poprzeć mogę kilkuletnim doświadczeniem w konstrukcji tego typu urządzeń, którego owocem były choćby takie projekty jak publikowane na łamach EP projekty TIDex (EP 05/2013 i KIT AVT5395) i TripCo (EP 07/2013 i KIT AVT5405). Po cóż w takim razie kolejny?
Odpowiedź jest prosta! Prezentowane wcześniej urządzenia, mimo, że cechowały się zbliżoną do bieżącego projektu funkcjonalnością, nie były rozwiązaniami uniwersalnymi w każdym tego słowa znaczeniu. TIDex współpracować mógł tylko i wyłącznie z pojazdami marki Opel, jako że korzystał z wbudowanego w pojazd, oryginalnego wyświetlacza pokładowego, zaś TripCo, mimo iż wyposażony był w szalenie atrakcyjny interfejs użytkownika zbudowany przy użyciu nowoczesnego, graficznego wyświetlacza OLED, właśnie z tego powodu (a dokładnie ceny takiego elementu i sposobu jego podłączenia) nie był w zasięgu przeciętnego Kowalskiego!
Zbierając wieloletnie doświadczenia w przedmiotowej materii, postanowiłem zaprojektować nowe urządzenie, które to musiało spełniać pewne, wstępne i nienaruszalne założenia funkcjonalno/instalacyjne. W związku z tym, nowy projekt musiał spełniać następujące kryteria:
- Pełna funkcjonalność typowego komputera pokładowego.
- Czytelny, intuicyjny i atrakcyjny (najlepiej graficzny) interfejs użytkownika.
- Możliwość personalizacji urządzenia poprzez dobór wyświetlacza o żądanym kolorze podświetlenia jak i kolorze wyświetlanej treści.
- Możliwość regulowania jasności podświetlenia wyświetlacza graficznego zgodnie z ustawieniem jasności podświetlenia zegarów pojazdu.
- Łatwość montażu uzyskana poprzez zastosowanie łatwo dostępnych, niedrogich i prostych w montażu elementów elektronicznych.
- Niewielkie wymiary zewnętrzne.
- Łatwość instalowania uzyskana poprzez zastosowanie pojedynczego złącza połączeniowego o niewielkiej liczbie wyprowadzeń (a więc i liczbie niezbędnych sygnałów sterujących).
- Niska cena całego urządzenia na poziomie 100-120 zł!
Ponadto, postawiłem dość wysokie wymagania dotyczące funkcjonalności komputera pokładowego, którego to zdecydowałem się wyposażyć w następującą funkcjonalność:
- Pomiar i pokazywanie temperatury wewnątrz i na zewnątrz pojazdu oraz ostrzeżenia o śliskiej nawierzchni (przy temperaturze zewnętrznej niższej niż 3°C).
- Funkcja automatycznego powiadamiania o konieczności włączenia świateł mijania (po osiągnięciu przez pojazd prędkości powyżej 5 km/godz.).
- Pokazywanie chwilowej prędkości pojazdu (w km/godz.).
- Pokazywanie średniej prędkości pojazdu na przejechanym odcinku drogi (w km/godz.).
- Pokazywanie maksymalnej prędkości pojazdu na przejechanym odcinku drogi (w km/godz.).
- Pokazywanie prędkości obrotowej silnika (w obr./min).
- Pokazywanie chwilowego zużycia paliwa (w l/godz. dla prędkości ≤ 5 km/godz. oraz l/100 km dla pozostałych prędkości).
- Pokazywanie średniego zużycia paliwa (w l/100 km).
- Pokazywanie paliwa pozostającego w baku pojazdu(w litrach).
- Pokazywanie przewidywanego zasięgu pojazdu na paliwie pozostającym w baku pojazdu (w km).
- Pokazywanie przejechanego dystansu od ostatniego zerowania stanu licznika (w km).
- Pokazywanie liczby uruchomień zapłonu.
- Pokazywanie aktualnego czasu i daty (z zastosowaniem mechanizmu podtrzymania zasilania).
- Cykliczne (co 1 minutę) pokazywanie imienin dla bieżącego dnia roku (wbudowany kalendarz imienin).
Czy możliwe jest zbudowanie urządzenia spełniające powyższe kryteria a dodatkowo wyróżniającego się tak niskim kosztem implementacji? Jak najbardziej, a by się o tym przekonać wystarczy spojrzeć na schemat ideowy komputera samochodowego Mee pokazany na rysunku 1.
Komputer zbudowano z użyciem mikrokontrolera firmy Atmel typu ATmega32A-PU, zegara czasu rzeczywistego typu MCP7940M-I/P (Microchip) wyposażonego w mechanizm awaryjnego przełącznika zasilania oraz graficznego wyświetlacza LCD o rozdzielczości 122×32 piksele wyposażonego w sterownik ekranu NJU6450A (odpowiednik SED1520) pełniącego rolę graficznego interfejsu użytkownika GUI.
Mikrokontroler, jak to zwykle bywa, stanowi "serce" niniejszego sterownika i realizuje całą, założoną funkcjonalność urządzenia posiłkując się w tym celu szeregiem wewnętrznych modułów peryferyjnych. Mikrokontroler jest taktowany zewnętrznym rezonatorem kwarcowym 4,194 MHz, dzięki czemu jest zapewniona duża dokładność pomiarów czasu, niezbędna z punktu widzenia zastosowanych mechanizmów sprzętowo-programowych realizujących funkcje pomiarowe oraz mały pobór mocy ze źródła zasilania.
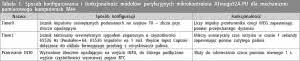
Tabela 1. Sposób konfigurowania i funkcjonalność modułów peryferyjnych mikrokontrolera ATmega32A-PU dla mechanizmu pomiarowego komputerach Mee
W celu realizacji założonej funkcjonalności, w programie obsługi niniejszego sterownika, wykorzystano dwa sprzętowe układy czasowo-licznikowe znajdujące się "na pokładzie" mikrokontrolera oraz jedno przerwanie zewnętrzne. Sposób konfiguracji wspomnianych modułów peryferyjnych oraz realizowaną przez nie funkcjonalność pokazano w tabeli 1.
Co bardziej dociekliwi Czytelnicy mogą zapoznać się z listingiem wszystkich funkcji, które odpowiedzialne są za realizację wspomnianego mechanizmu pomiarowego, a które pokazano na listingu 1.
Dodatkowo, w programie obsługi urządzenia, wykorzystano także ostatni, dostępny układ czasowo-licznikowy mikrokontrolera, Timer2 został skonfigurowany do pracy w trybie CTC. Jego zadaniem jest generowanie cyklicznych przerwań systemowych (co 10 ms) służących mechanizmowi nieblokującej obsługi klawiatury użytkownika (przyciski PLUS, MODE i MINUS) stanowiącej element interfejsu GUI.
Dzięki zastosowaniu tego typu rozwiązania, program obsługi aplikacji urządzenia nie wykorzystuje żadnych z wbudowanych w kompilator GCC opóźnień, co zapewnia jego bezproblemową pracę, jak i możliwość prostej detekcji czasu naciśnięcia przycisku (krótki/długi/przytrzymanie itd.), dzięki czemu udało się w sposób znaczący zoptymalizować sposób obsługi całego urządzenia zwiększając tym samym ergonomię pracy.
Tak jak pokazano w tab. 1, urządzenie dokonuje w czasie każdej jednej sekundy pomiaru sumarycznej liczby impulsów doprowadzanych na wejście T0 mikrokontrolera z przetwornika drogi pojazdu jak i pomiaru sumarycznego czasu wtrysków, których to sygnał doprowadzony jest na wejście przechwytujące licznika Timer1 (wejście ICP1).
W celu realizacji drugiej z funkcjonalności zaprojektowano kompletny i bezpieczny układ wejściowy (przy użyciu popularnego optoizolatora LTV817) formujący sygnał wtryskiwacza dla potrzeb wejściowych obwodów mikrokontrolera. Na listingu 2 przedstawiono wzory zaczerpnięte bezpośrednio z programu obsługi aplikacji a służące obliczeniu wszystkich parametrów rzeczywistych komputera pokładowego.
Czy nie daje Wam do myślenia wzór na obliczenie dostępnego dystansu availableDistance? Przecież na pierwszy rzut oka, te wszystkie dzielenia dałoby się uprościć? Właśnie! Na pierwszy rzut oka, jednak zawsze należy mieć na uwadze fakt, na jakiego rodzaju zmiennych operujemy i w jakim zakresie. W tym wypadku zmienne oraz wynik obliczeń są 32-bitowe.
Gdyby nie wprowadzono wstępnego dzielenie zmiennej Accu.remainingFuel przez 1000, a zmiennej Accu.Distance przez 10, to szybko przekroczylibyśmy 32-bitowy wynik mnożenia z licznika ułamka w przedstawionym wzorze, co skutkowałoby niepoprawnym wynikiem obliczeń. To częsty błąd początkujących programistów, więc zwracam szczególną uwagę na zakresy zmiennych oraz wyników poszczególnych obliczeń.
Idąc dalej, uważny Czytelnik z pewnością zauważy pewną "subtelność" dotyczącą sposobu zasilania mikrokontrolera polegającą na implementacji prostego układu chwilowego podtrzymania zasilania zbudowanego przy użyciu diody Schottky D1 oraz bloku kondensatorów elektrolitycznych C10...C12. W jakim celu wprowadzono tego typu rozwiązanie sprzętowe?
Urządzenie oblicza i wyświetla średnie wartości zużycia paliwa i prędkości, objętość paliwa pozostającego w baku pojazdu oraz pokonany dystans. Jak łatwo się domyślić i co potwierdzają wzory podane powyżej, w celu wyznaczenia wspomnianych wartości obliczeniowych jest niezbędna znajomość całkowitego zużycia paliwa oraz dystansu od momentu wyzerowania stosownych liczników, a co za tym idzie, staje się niezbędny mechanizm akumulowania mierzonych wartości nawet po zaniku napięcia zasilającego (po wyłączeniu zapłonu).
Mikrokontroler ATmega32A-PU dysponuje nieulotną pamięcią EEPROM, jednak ma ona ograniczoną (zwykle do ok. 100 tys.) liczbę gwarantowanych cyklów zapisu. W takim razie jak i kiedy dokonywać zapisu niezbędnych wartości obliczeniowych by nie spowodować szybkiego uszkodzenia tej pamięci? Odpowiedź wydaje się dość prosta, choć samo rozwiązanie - moim zdaniem - całkiem interesujące.
Niezbędne wartości obliczeniowe "zebrane" w specjalną strukturę danych zaopatrzoną w sumę kontrolną CRC8 (pozwalającą na sprawdzenie integralności danych) zapisywane są każdorazowo przy wyłączaniu zapłonu (oraz cyklicznie, co 1 sekundę, w pamięci RAM układu RTC). Do wykrycia momentu wyłączania zapłonu zastosowano wbudowany w mikrokontroler przetwornik A/C pracujący w trybie Free Running i monitorujący napięcie Vbak, czyli napięcie zasilające wyłącznie mikrokontroler (po zaniku zasilania dioda D1 zapewnia separację zasilania mikrokontrolera od reszty urządzenia a kondensatory C10...C12 zapewniają odpowiedni czas podtrzymania zasilania).
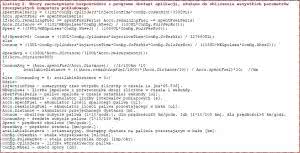
Listing 2. Wzory zaczerpnięte bezpośrednio z programu obsługi aplikacji, służące do obliczenia wszystkich parametrów rzeczywistych komputera pokładowego
Na pierwszy "rzut oka" nie wydaje się, by komputer pokładowy w jakikolwiek sposób używał przetwornika A/C, ponieważ żaden z kanałów wejściowych nie jest przez niego używany. To prawda. Patrząc na schemat układu i nie mając do dyspozycji listingu programu można by wysnuć taki wniosek. Jest jednak inaczej.
Przetwornik A/C mierzy wewnętrzne napięcie odniesienia VBG=1.22 V (wartość dla mikrokontrolera ATmega32A-PU), dzięki temu, iż wewnętrzny, analogowy multiplekser przetwornika może zostać właśnie w ten sposób ustawiony. Napięciem odniesienia jest z kolei napięcie zasilające mikrokontroler dostarczane na wyprowadzenie AVCC (czyli nasze Vbak). Spadek tego napięcia, podczas wyłączania zapłonu, powoduje wzrost wartości wyniku przetwarzania zgodnie z wyrażeniem (korzystamy z 8-bitowej rozdzielczości przetwornika): VADC = (VBG *256)/ Vbak.
Procedura obsługi przerwania przetwornika A/C każdorazowo sprawdza czy nie został przekroczony zdefiniowany wcześniej próg obliczeniowy, a jeśli ma to miejsce, to inicjuje proces zapisywania danych krytycznych do wbudowanej pamięci EEPROM, po czym czeka, aż napięcie zasilania spadnie do poziomu zerowania mikrokontrolera, które jest wykonywane przez blok BOD (typowo przy wartości 2,7 V).
Wspomniany próg zadziałania ustawiono na 4,3 V, co oznacza, że czas opadania napięcia zasilającego od wartości 4,3 V do 2,7 V jest czasem, w którym mikrokontroler musi przeprowadzić zapis wszystkich danych krytycznych - w naszym wypadku 24 bajtów danych. Jak pokazały testy praktyczne, zastosowanie wspomnianego wcześniej rozwiązania sprzętowego (dioda D1 i kondensatory C10...C12) i mechanizmów programowych zapewnia 100% skuteczność zapisu danych z bardzo dużym marginesem czasowym.
Wykres zależności napięcia podtrzymania w funkcji czasu w momencie wyłączenia zapłonu pokazano na rysunku 2. Czas dostępny na zapis danych to około 350 ms, co dla wymaganej, maksymalnej wartości rzędu 190 ms (obliczonej i potwierdzonej rzeczywistym pomiarem) daje spory margines bezpieczeństwa. Co oczywiste, potencjalne uszkodzenie w bloku sprzętowym odpowiedzialnym za podtrzymanie napięcia zasilającego (np. uszkodzenie kondensatorów elektrolitycznych C10...C12) będzie skutkowało błędnymi zapisami pamięci EEPROM, gdyż dołączana (do struktury danych) suma kontrolna nie będzie zgodna z oczekiwaną.
W takim wypadku oprogramowanie w pierwszej kolejności odczyta kopię struktury danych akumulatorów obliczeniowych z pamięci RAM zegara RTC, do której cyklicznie ją zapisuje i której zawartość podtrzymywana jest nawet w czasie wyłączenia zapłonu (dzięki napięciu BATT), a następnie ponownie sprawdzi integralność odczytanych danych.
Jeśli nawet kopia tychże danych okaże się błędna (np. od pojazdu na chwile odłączono akumulator lub sam komputer pokładowy został odłączony od zasilania BATT), urządzenie poinformuje o tym fakcie użytkownika wyświetlając komunikat "Save Error" tuż po włączeniu zasilania, w czasie sprawdzania integralności tychże danych oraz wyzeruje je wszystkie, ponieważ nie będzie wtedy pewności, że ich wartości są prawidłowe. Procedury konfigurowania przetwornika A/C oraz obsługi jego przerwania pokazano na listingu 3.
Na koniec kilka słów uwagi na temat zastosowanego układu zegara czasu rzeczywistego - układu firmy Microchip MCP7940. Pojawia się pytanie, dlaczego zastosowałem taki "nietypowy" układ zegara RTC, skoro zwykle w to miejsce wybierane są peryferia znacznie bardziej popularne.
Odpowiedź jest prosta: cena, która oscyluje na poziomie poniżej 1$ za sztukę przy zakupie detalicznym! Pamiętamy przecież, iż jednym z założeń projektu była możliwie najniższa cena końcowa, stąd proces doboru każdego z elementów składowych został dobrze przemyślany, by spełnić wspomniane wymagania.
Układ scalony zegara MCP7940 oprócz standardowego zegara i kalendarza (z automatyczną korekcją dla lat przestępnych) następującą funkcjonalność:
Możliwość ustawienia dwóch, niezależnych alarmów o bardzo rozbudowanej funkcjonalności, jeśli chodzi o dostępne kryteria wywołujące alarm, w tym możliwość zmiany stanu wyjścia MFP, na skutek wywołania alarmu.
- Możliwość programowej kompensacji niedokładności rezonatora kwarcowego (w zakresie -127...+127 ppm.
- Możliwość generowania częstotliwości wzorcowej na wyprowadzeniu MFP z zakresu: 1 Hz, 4096 Hz, 8192 Hz, 32768 Hz.
- Możliwość programowego, niezależnego (od alarmów i generatora częstotliwości wzorcowej) sterowania wyjściem MFP.
- 64 bajty dodatkowej pamięci RAM dostępnej dla aplikacji użytkownika.
Nie wdając się niepotrzebnie w szczegóły karty katalogowej zaprezentuję kluczowe funkcje narzędziowe niezbędne do nawiązania współpracy z naszym układem zegara RTC. Na listing 1 pokazano plik nagłówkowy, który tym razem jest dość krótki, gdyż nie zależało mi na ujęciu w jego treści całej funkcjonalności układu (tzn. możliwości alarmowania i kompensacji niedokładności rezonatora kwarcowego).
Dla poprawienia czytelności kodu wprowadzono dwa nowe typy strukturalne odpowiedzialne za przechowywanie czasu i daty zegara RTC. Na listingu 4 pokazano kluczowe funkcje przeznaczone do obsługi zegara MCP7940: funkcję odpowiedzialną za skonfigurowanie układu, funkcje przeznaczone do zapisu i do odczytu godziny oraz daty, funkcje przeznaczone do odczytu i zapisu wbudowanej w układ MCP7940 pamięci RAM przeznaczonej na dane użytkownika.
Dodatkowo, na wspomnianym listingu, pokazano dość ciekawą a niezmiernie prostą funkcję (rzadko implementowaną), która umożliwia określenie czy rok podany jako argument wywołania (w zakresie 0...99) jest przestępnym czy też nie. Funkcja ta jest wykorzystywana do wyszukiwania imienin w kalendarzu imion, aby nie pominąć 29 lutego.
Wracając do tematu funkcji obsługujących zegar RTC warto zauważyć, iż w tym konkretnym rozwiązaniu, rozdzielono mechanizmy dotyczące daty i godziny, gdyż nie zawsze jest celowe operowanie tymi dwoma ustawieniami, w związku z czym nie ma powodu, aby zwiększać ruch na magistrali I²C.
Już zupełnie na koniec dodam, iż zdecydowaną większość pamięci programu aplikacji zajęły wzorce obrazków wyświetlanych w ramach graficznego interfejsu użytkownika, tablica używanych czcionek oraz wbudowany kalendarz imienin, którego stałe znakowe zajmują ponad 10 kB pamięci Flash! Bez tej ostatniej funkcjonalności, program obsługi aplikacji swobodnie zmieściłby się w pamięci programu mikrokontrolera ATmega16A-PU, lecz z uwagi na niewielką różnicę w cenie obu mikrokontrolerów (ok. 4 zł), ostatecznie nie zrezygnowałem z tej niespotykanej opcji.
Wykaz elementówRezystory: (0,125 W) Kondensatory: Półprzewodniki: Inne: |
Montaż
Schemat montażowy komputera pokładowego Mee pokazano na rysunku 3. Zbudowano go na dwustronnej płytce drukowanej, z elementów przeznaczonych wyłącznie do montażu przewlekanego, przy czym należy zauważyć, iż elementy te montowane są po obu stronach laminatu. Co bardzo ważne, w przypadku środowisk o sporej liczbie zaburzeń, jakim bez wątpienia jest instalacja samochodowa, zadbano o odpowiednie prowadzenie masy i sygnałów krytycznych.
Montaż rozpoczynamy od wlutowania rezystorów, następnie montujemy kondensatory, elementy mechaniczne takie jak przyciski i złącze goldpin przeznaczone do podłączenia wyświetlacza graficznego, a na samym końcu elementy półprzewodnikowe, które można umieścić w podstawkach. Jako ostatnie należy wlutować gniazdo połączeniowe CON - montujemy je od spodu (BOTTOM).
Opcjonalnie, aby zmniejszyć odległość wyświetlacza LCD od obwodu drukowanego, kondensatory elektrolityczne C2, C4, C10...C12 mogą być zamontowane od spodu (BOTTOM). Na rysunkach 4 i 5 pokazano wygląd prototypowego obwodu drukowanego zmontowanego komputera pokładowego Mee, bez wyświetlacza LCD.
Podłączenie
Podłączenie sterownika powinno być wykonane przez doświadczonego elektryka bądź elektronika samochodowego przy odłączonym akumulatorze. Urządzenie należy zamontować w suchym miejscu, z dala od urządzeń elektrycznych lub elektronicznych, której działanie mogłoby zakłócić funkcjonowanie sterownika (typu sterownik silnika ECU, moduł kontroli nadwozia BCM czy alarm).
Najlepiej, aby komputer był zamontowany w odpowiedniej, najlepiej ekranowanej obudowie chroniącej go przed zwarciem, zawilgoceniem, uszkodzeniem mechanicznym czy zakłóceniami EMI. W celu wykorzystania wszystkich, dostępnych funkcji urządzenia, sterownik należy dołączyć tylko do dwóch (co nie jest bez znaczenia dla początkujących elektroników) podzespołów samochodu:
- Złącza radioodbiornika: to podstawowe podłączenie umożliwiające zasilenie układu po włączeniu stacyjki (+12 V), podtrzymanie pracy zegara RTC (BATT), doprowadzenie sygnału prędkości pojazdu (WEG) oraz napięcia do podświetlenia wyświetlacza graficznego (ILL+).
- Wtryskiwacza paliwa: to połączenie umożliwia realizację funkcji komputera pokładowego (INJ+, INJ-).
Ponadto, urządzenie Mee wyposażono w możliwość dołączenia dwóch scalonych termometrów cyfrowych typu DS18S20 (lub DS1820), dzięki którym jest możliwy pomiar temperatury wewnątrz i na zewnątrz pojazdu. Termometry te należy dołączyć do złącza CON (jego pinów oznaczonych GND, +5 V i 1WIRE) najlepiej za pomocą 3-żyłowego, ekranowanego odcinka przewodu.
Należy eksperymentalnie dobrać miejsce zamocowania obu czujników, aby odwzorować średnią temperaturę panującą wewnątrz pojazdu oraz temperaturę zewnętrzną. Dla czujnika temperatury wewnętrznej unikać należy jego montażu w pobliżu nawiewów, drzwi, okien itp. Najlepszym miejscem w tym wypadku, wydaje się być tylna część tunelu środkowego, bądź kieszeń-schowek pod radioodbiornikiem.
Z kolei, dla czujnika temperatury zewnętrznej (który to należy zabezpieczyć przed działaniem warunków zewnętrznych, takich jak wilgoć i woda) najlepszym miejscem montażu wydaje się przestrzeń za przednim zderzakiem pojazdu. Wygląd typowych złącz ISO radioodbiornika wraz z zaznaczeniem interesujących nas wyprowadzeń pokazano na rysunku 6.
Co ciekawe, w zależności od marki producenta pojazdu, piny o numerach 4 i 7 (oznaczone +12 V i BATT) mogą być zamienione miejscami w stosunku do pokazanych na rysunku 6 opisów, w związku z czym ich rzeczywiste funkcje należy ustalić doświadczalnie. A zatem, napięcie na pinie +12 V powinno występować wyłącznie po włączeniu zapłonu (przekręceniu kluczyka), zaś na pinie BATT permanentnie (tzn. dopóki akumulator podłączony jest do instalacji pojazdu).
Napięcie na pinie ILL+ to zwyczajowo przebieg prostokątny o amplitudzie ok. 12 V i wypełnieniu zależnym od ustawienia pokrętła regulującego jasność podświetlenia zegarów pojazdu (jak i innych akcesoriów, które posiadają elementy podświetlone). Co oczywiste, w naszym wypadku, wykorzystywane jest do regulacji jasności podświetlenia wyświetlacza urządzenia Mee. Jeśli nie zależy nam na takiej funkcjonalności, pin ILL+ należy połączyć na stałe z pinem +12 V złącza CON.
Sposób dołączenia urządzenia do wtryskiwacza paliwa
Połączenie w tym zakresie należy wykonać nader starannie zachowując przy tym dużą ostrożność, by nie doprowadzić do zwarcia przewodów zasilających wtryskiwacz, co mogłoby skutkować uszkodzeniem wyjściowych obwodów sterujących elektronicznego układu sterującego pracą silnika ECU. Każdy wtryskiwacz ma dwa wyprowadzenia.
Pierwsze, to stały sygnał +12 V, który zostaje podany po przekręceniu kluczyka stacyjki i który to należy dołączyć do wejścia INJ+ naszego urządzenia. Drugie, to sygnał sterujący z modułu ECU (komutowana masa), który to z kolei podłączyć należy do wejścia INJ-.
Wspomniane przewody należy starannie zabezpieczyć przed możliwością ewentualnego przetarcia izolacji i powstania zwarcia - dotyczy to zwłaszcza wszelkiego rodzaju otworów przelotowych, przez które zostaną one przeprowadzone.
Aby maksymalnie zabezpieczyć wejściowy układ pomiarowy czasu wtrysku od zaburzeń (np. od będącej zwykle w pobliżu listwy zapłonowej) najlepiej zastosować dwużyłowy przewód ekranowany o odpowiednim przekroju zaś ekran tego przewodu podłączyć po obu stronach do masy pojazdu.
Możliwe jest także podłączenie układu formującego impulsy wtryskiwaczy paliwa bezpośrednio do odpowiedniego wyjścia sterownika silnika ECU, na którym to występuje przebieg sterujący pracą wtryskiwaczy. Wtedy należy odpowiednio zmniejszyć wartość rezystora R8 ustalającego prąd diody LED transoptora LTV817.
Aby ułatwić zainstalowanie komputera w pojeździe, po stronie wyprowadzeń obwodu drukowanego, a więc również złącza CON, znalazł się opis poszczególnych jego wyprowadzeń. Sposób dołączenia poszczególnych wyprowadzeń złącza CON do instalacji pojazdu pokazano na rysunku 7.
Obsługa
Komputer pokładowy Mee jest urządzeniem, które zwykle będzie obsługiwane podczas jazdy samochodem, więc ergonomia i prostota obsługi oraz czytelność interfejsu użytkownika była podstawowym kryterium przy konstruowaniu stosownych procedur sterujących. Zgodnie z tymi podstawowymi założeniami, na płytce sterownika przewidziano jedynie 3 elementy sterujące (microswitche) umownie oznaczone PLUS, MINUS i MODE).
Jak łatwo się domyślić, przyciski PLUS i MINUS służą do zmiany aktualnie wyświetlanego ekranu Menu lub też do regulacji edytowalnych parametrów pracy urządzenia (jeśli jesteśmy w trybie edycji jakiegoś parametru). Dodatkowo, w większości trybów pracy długotrwałe przytrzymanie przycisków PLUS i MINUS zwiększa szybkość regulacji wybranego parametru urządzenia.
Oprócz wspomnianej powyżej funkcjonalności, przyciski PLUS i MODE mają dodatkowe funkcje: krótkie przyciśnięcie przycisku MODE powoduje zapisanie bieżącego trybu pracy urządzenia w nieulotnej pamięci układu by tryb ten stał się aktywnym trybem pracy po ponownym włączeniu zapłonu, zaś długie przyciśnięcie przycisku PLUS powoduje wykasowanie liczników dystansu i średnich wartości obliczeniowych. Nie są to jednak wszystkie funkcje wspomnianych switchy, gdyż ich funkcjonalność zależna jest od aktualnego trybu pracy komputera.
Na rysunku 8 pokazano wszystkie dostępne tryby pracy sterownika, natomiast na rysunku 9 pokazano diagram obrazujący strukturę menu jak również sposób obsługi urządzenia (symbole przycisków wypełnione kolorem czarnym oznaczają długie naciśnięcie wybranego przycisku).
Warto zauważyć, że funkcja pokazywania ilości dostępnego paliwa w baku nie korzysta z sygnału informującego o rzeczywistym poziomie paliwa, gdyż jej implementacja w takim przypadku, skalowanie jak i samo podłączenie sterownika do instalacji pojazdu byłoby dość kłopotliwe. Mechanizm jej działania jest bardzo prosty i zakłada każdorazowe uzupełnianie bieżącego odczytu o ilość zatankowanego paliwa, co jest możliwe poprzez wejście w tryb edycji paliwa dostępnego w baku (długie wciśnięcie przycisku MODE w trakcie wyświetlania stosownego menu).
Reasumując, po każdym tankowaniu pojazdu należy wejść w edycję dostępnego paliwa i zwiększyć jego ilość (regulacja następuje o pełne litry paliwa). Mechanizm pomiarowy komputera pokładowego będzie następnie odejmował od wartości dostępnego paliwa zużywane paliwo, co umożliwia realizację wspomnianej funkcjonalności.
Ustawienia fuse-bitów: |
Nastawy i tryb kalibrowania stałej wtryskiwacza
Komputer pokładowy wyposażono w specjalny tryb pracy służący do konfigurowania. Dzięki niemu możemy określić pewne niezbędne parametry regulacyjne nieodzowne z punktu widzenia funkcjonalności. Ten tryb pracy uruchamiamy poprzez naciśnięcie i przytrzymanie przycisku MODE podczas włączania urządzenia (czyli zapłonu pojazdu). W tym trybie pracy urządzenia możemy określić wielkość następujących stałych niezbędnych w procesie obliczania zużycia paliwa, prędkości jazdy oraz drogi:
- Stała wtryskiwacza (w [ml/min]): jest to wielkość charakterystyczna dla każdego wtryskiwacza elektronicznego wtrysku paliwa informująca nas o ilości paliwa, jakie może on wprowadzić do komory spalania w jednostce czasu (przy założeniu 100% czasu otwarcia zaworu i stałym, charakterystycznym dla każdego wtryskiwacza ciśnieniu zasilającym).
- Stała przetwornika drogi (impulsatora, w [imp/obr]): jest to wielkość charakterystyczna dla każdego impulsatora informująca nas o liczbie impulsów przypadających na 1 obrót koła (osi); dla przykładu w większości nowych modeli marki Opel jest to wartość 29 imp./obr.
- Obwód opony (w [cm]).
- Liczba cylindrów (a więc i liczba wtryskiwaczy zamontowanych w silniku pojazdu).
Wspomniane stałe można, co prawda znaleźć w Internecie posiłkując się wszelkiego rodzaju forami o tematyce motoryzacyjnej lub elektronicznej, lecz wydaje się, że lepszym sposobem na ich pozyskanie jest wyznaczenie ich na drodze empirycznej. Dla przykładu, obwód opony, a w zasadzie drogę, jaką pokona pojazd w czasie jednego, pełnego obrotu koła, możemy wyznaczyć dość prosto.
W tym celu zaznaczamy (np. kredą) najniżej położone miejsce styku opony z powierzchnią drogi, następnie standardowo obciążony pojazd przetaczamy, aby koło wykonało jeden pełny obrót, po czym mierzymy pokonany odcinek drogi. Wszystkie wprowadzone wartości zostaną zachowane w nieulotnej pamięci EEPROM urządzenia, po czym sterownik przejdzie do normalnego trybu pracy.
Niestety, jak pokazała praktyka, pewnych trudności może czasami nastręczać znalezienie parametrów stosowanych w naszym pojeździe wtryskiwaczy, jako że elementy te są często wykonywane na zamówienie producenta pojazdu i na próżno szukać ich oznaczeń na stronach producentów stosownych podzespołów. Dlatego przewidziano pewien mechanizm, za pomocą którego komputer jest w stanie samodzielnie wyznaczyć poszukiwaną stałą na podstawie informacji o zużytym paliwie i pomiarze sumarycznego czasu wtrysków.
Do tego celu przewidziano specjalny tryb kalibracyjny, który może zostać uruchomiony poprzez naciśnięcie i przytrzymanie przycisku MINUS podczas włączania urządzenia, co zostanie zasygnalizowane wyświetleniem okna informacyjnego z komunikatem "Calibr. ON". Ponowne wykonanie wspomnianych czynności (podczas ponownego włączania urządzenia z uruchomionym wcześniej trybem kalibracyjnym) powoduje obliczenie żądanej stałej wtryskiwacza a następnie opuszczenie procesu kalibracji sygnalizowane wyświetleniem okna informacyjnego z napisem "Calibr. OFF".
Co oczywiste, do czasu zakończenia procesu kalibracji nie są dostępne następujące wartości obliczeniowe: chwilowe i średnie zużycie paliwa oraz ilość paliwa dostępnego w baku pojazdu (jest to sygnalizowane wyświetleniem napisu "-" w odpowiednich polach wspomnianych wartości). Aby przeprowadzenie procesu kalibracji miało w ogóle sens należy zastosować następujący algorytm postępowania:
- Zużyć całe, dostępne paliwo, aż do zaświecenia się lampki sygnalizującej tzw. rezerwę.
- Zatankować 20 litrów paliwa.
- Uruchomić procedurę kalibracji.
- Zużyć całe, dostępne paliwo (zatankowane wcześniej 20 l), aż do ponownego zaświecenia się lampki sygnalizującej tzw. rezerwę paliwa.
- Zakończyć procedurę kalibracji.
Po wykonaniu tych czynności komputer obliczy i zapisze, w nieulotnej pamięci EEPROM mikrokontrolera, wartość stałej wtryskiwacza, po czym przejdzie do normalnego trybu pracy. Gdyby obliczona przez sterownik wartość stałej wtryskiwacza powodowała zaniżanie lub zawyżanie rzeczywistego spalania paliwa, w każdej chwili możemy dokonać odpowiedniej jej korekty poprzez wywołanie nastaw i zwiększenie (w przypadku zaniżania spalania) lub zmniejszenie (w przypadku zawyżania spalania) wspomnianej wartości.
Należy zaznaczyć, iż tak jak w wypadku oryginalnych rozwiązań typu "komputer pokładowy", obliczane wartości zużycia paliwa są obarczone pewnym acz niewielkim błędem wynikającym choćby z założenia stałego ciśnienia zasilającego wtryskiwacz czy też z zaokrągleń obliczeniowych, jednak testy praktyczne pokazały, iż maksymalny błąd pomiarowy jest na poziomie 0,5 litra na całą pojemność baku pojazdu, czyli ok. 1% (w tym wypadku było to 45 litrów).
Dla porządku przedstawię typy wyświetlaczy, które to można zastosować w komputerze pokładowym, a których rodzaje - biorąc pod uwagę kolor treści i tła - pokazano na rysunku 10. Należy jednak mieć na uwadze, że niektóre z nich (zwłaszcza te, w wykonaniu "negatywowym") cechuje dość niska częstotliwość odświeżania w przypadku pracy w niskich temperaturach (nawet poniżej 10°C), co powoduje lekkie smużenie przy zmianie wyświetlanej treści. Niestety, jak to w życiu bywa, coś za coś! Dzięki temu uzyskujemy bardzo atrakcyjną cenę urządzenia, ponieważ cena samego wyświetlacza stanowi prawie połowę ceny całego urządzenia!
Robert Wołgajew, EP