Projektowanie płytek. Ekranowanie i powody ekranowania. cz. 2
Środa, 01 Lipiec 2009
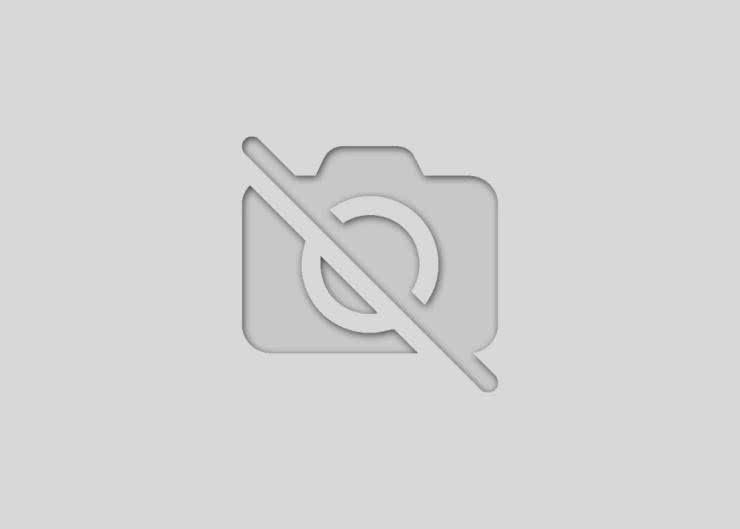
Wraz z rozwojem elektroniki znacząco zwiększyło się natężenie tak
zwanego smogu elektronicznego. Skutkiem tego, na projektowane
urządzenia zostały nałożone specjalne normy emisji, jak
i wrażliwości, które każde z nich powinno bezwzględnie spełnić.
W tej części cyklu zajmę się omówieniem sposobów ekranowania
stosowanych w nowoczesnym projektowaniu obwodów drukowanych.
72 ELEKTRONIKA PRAKTYCZNA 7/2009
NOTATNIK KONSTRUKTORA
Dodatkowe
materiały na CD
Projektowanie płytek (2)
Ekranowanie i powody
ekranowania
Prędzej czy później, każdy projektant spotka
się z problemem zabezpieczenia przed zakłóce-
niamiwrażliwychczęściobwodu.Przyczynąjest
obniżenie odporności na zakłócenia poszczegól-
nych komponentów, a powodem tego obniżenia
jest paradoksalnie ? postęp technologiczny. Roz-
różnia się trzy główne źródła owej zwiększonej
wrażliwości: miniaturyzacja struktur kompo-
nentów, obniżenie napięć zasilających a tym
samym zmiana wartości napięć- progów przełą-
czania oraz zwiększenie częstotliwości pracy.
Postępu technologicznego nie można po-
wstrzymać, natomiast projektant może cał-
kiem skutecznie chronić wrażliwe komponen-
ty przed wpływem niepożądanego promienio-
wania elektromagnetycznego. Należy jednak
wspomnieć, iż stosowanie technik ekranowa-
nia bez odpowiedniego ?ltrowania nie ma sen-
su. Jedynie równoczesne stosowanie obu tych
technik przynosi pozytywne rezultaty.
Przyczyny ekranowania na PCB
Istnieje kilka przyczyn przeniesienia ekra-
nowania urządzenia na poziom obwodu druko-
wanego. Najbardziej istotnym powodem zmia-
ny techniki ekranowania jest niemożliwość
ekranowania za pomocą obudowy wrażliwych
części obwodu drukowanego przed oddzia-
ływaniem fal wielkiej częstotliwości. Kolejne
powody to:
? ekranowanie przenoszone jest na najniższy
poziom montażu,
? ekranowanie nie zwiększa znacząco wagi
urządzenia,
? pozwala na większą gęstość upakowania
elementów, niż inne metody ekranowania,
? jest to najlepsza metoda ekranowania za-
pewniającą wysoką ochronę wrażliwych
komponentów pracujących w tzw. hała-
śliwym środowisku, czyli w pobliżu anten
urządzeń do transmisji bezprzewodowej,
? poprawa wyglądu urządzeń (przeniesienie
anten do wnętrza obudowy, bądź wręcz
zintegrowanie ich z drukiem).
Wraz z rozwojem elektroniki znacząco zwiększyło się natężenie tak
zwanego smogu elektronicznego. Skutkiem tego, na projektowane
urządzenia zostały nałożone specjalne normy emisji, jak
i wrażliwości, które każde z nich powinno bezwzględnie spełnić.
W tej części cyklu zajmę się omówieniem sposobów ekranowania
stosowanych w nowoczesnym projektowaniu obwodów drukowanych.
często pomija się efekt tłumienia wynikający
ze zjawiska odbicia energii wewnątrz mate-
riału ekranu. Tłumienie absorpcyjne silnie
zależy od elektrycznych i magnetycznych
własności materiału ekranu, jego grubości,
częstotliwości pola.
W praktyce ekrany charakteryzowane są
przez dwa główne parametry: impedancję
oraz skuteczność ekranowania. O ile pierw-
szy parametr ma ścisły związek z częstotli-
wością pola oraz rodzajem wykorzystanego
materiału, o tyle na drugi ma wpływ kilka
interesujących czynników. Wśród nich nale-
ży wymienić: częstotliwość pola, strukturę
geometryczną, rodzaj pola (składowa elek-
tryczna czy magnetyczna), kierunek padania
pola. Skuteczność ekranowania wyrażana jest
w decybelach i określa stopień tłumienia od-
powiedniej składowej pola elektromagnetycz-
nego. Można ją wyznaczyć z następującego
wzoru:
KE
= 20 log (EZEW
/EWEW
)
gdzie:
KE
? skuteczność ekranowania,
EZEW
? natężenie składowej pola na zewnątrz
ekranu,
EWEW
? natężenie składowej pola wewnątrz
ekranu.
Ekranowanie wysoko-impedancyjnych
pól elektrycznych jest stosunkowo proste
i przy użyciu nawet cienkich ekranów moż-
na osiągnąć duże wartości współczynników
tłumienia. Tłumienie ekranów maleje ze
wzrostem częstotliwości. Paradoksalnie sku-
teczność ekranowania maleje ze wzrostem od-
ległości między źródłem i ekranem, ponieważ
zmniejsza się impedancja pola.
Ekranować, w zależności od potrzeb, moż-
na poszczególne komponenty, grupy kompo-
nentów, obszary płytki drukowanej, całą płytkę
lub całe urządzenie.
Parametry
Natężenie pola przechodzącego przez
ekran tłumione jest w wyniku odbicia i absorp-
cji energii. Tłumienie odbiciowe zależy od czę-
stotliwości, rodzaju pola, właściwości materia-
łu ekranu i odległości ekranu od źródła pola.
W teorii zjawisk falowych efekt odbi-
cia tłumaczy się niezgodnością impedancji
falowych ekranu i środowiska otaczającego
ekran. W rozważaniach praktycznych pomija
się zwykle, jako mały, efekt tłumienia wyni-
kający z odbicia energii wewnątrz materiału
ekranu.
Tłumienie absorpcyjne zależy od wła-
ściwości elektrycznych i magnetycznych
materiału ekranu, jego grubości oraz często-
tliwości, natomiast praktycznie nie zależy od
rodzaju pola padającego na ekran
Natężenie pola przechodzącego przez
ekran jest tłumione na skutek absorpcji ener-
gii i jej odbicia. Tłumienie odbiciowe zależy
od częstotliwości i rodzaju pola, własności
materiału ekranu, jak również odległości po-
między ekranem o źródłem pola. W praktyce
Rys. 1.
73ELEKTRONIKA PRAKTYCZNA 7/2009
Projektowanie płytek
Ekranowanie magnetycznych pól bliskich, zwłaszcza przy niskich
częstotliwościach, jest bardzo trudne i skuteczne rozwiązanie prowa-
dzi zawsze do masywnych, grubych ekranów wykonanych z materia-
łów ferromagnetycznych. Skuteczność ekranowania wzrasta w miarę
wzrostu częstotliwości. Odwrotnie niż w przypadku pola elektryczne-
go, impedancja pola magnetycznego rośnie wraz z odległością i dlatego
skuteczność ekranowania wzrasta przy większych odległościach między
źródłem i polem.
Segregacja
Terminem tym określa się zaawansowane techniki segregacji po-
szczególnych elementów tworzące bloki funkcjonalne obwodu w odpo-
wiednich rejonach płytki, tak aby było możliwe prawidłowe i optymalne
funkcjonowanie budowanego urządzenia. Proces ten należy prowadzić
od początku rzeczywistego procesu projektowego, gdy jeszcze nie rozpla-
nowaliśmy technik ?ltrowania i ekranowania.
Segregację rozpatruje się na dwóch płaszczyznach:
? Outsideworld?płaszczyznaobejmującazapewnienieodpowiedniego
poziomu EMC urządzenia uwzględniająca szkodliwe oddziaływania
środowiska zewnętrznego, jak i szkodliwego oddziaływania urządze-
nia na środowisko. Obejmuje ona np. zagadnienia odpowiedniego
?ltrowania sygnałów dostających się do obwodu poprzez wszelkiego
rodzaju wiązki przewodów.
? Inside world ? płaszczyzna ustalana w drugiej kolejności, gdy nastę-
puje podział bloków urządzenia na tak zwane szybkie - wysoko hała-
śliwe oraz wrażliwe ? wysokiej rozdzielczości.
Prawidłowo przeprowadzona segregacja zapewnia tak mechaniczne
jak i elektryczne odseparowanie od siebie poszczególnych obszarów ob-
wodu. Sytuację taką przedstawiono na rys. 1. Pomiędzy poszczególnymi
wydzielonymi obszarami znajduje się wolna przestrzeń, która powinna
być wypełniona masą (czyli najniższym potencjałem). Umożliwia ona
nałożenie ekranów w postaci puszek Faradya na poszczególne pakiety
komponentów.
Najczęstszym błędem popełnianym przez projektantów po przepro-
wadzeniu prawidłowej segregacji jest zaniedbanie utrzymania podziału
w dalszych krokach projektowych. Najprościej jest zapobiegać temu zja-
wisku już na etapie schematu. W zależności od możliwości środowiska
CAD, można podzielić urządzenie na bloki funkcjonalne lub symbo-
licznie wydzielać pakiety elementów za pomocą linii otaczających od-
powiednie bloki elementów w obrębie schematu. Wtedy w końcowym
etapie układania ścieżek w edytorze połączeń, liczba przejść pomiędzy
wydzielonymi strefami musi odpowiadać tym ze schematu.
Montaż
Istotnym zagadnieniem o jakim należy wspomnieć jest wykonawstwo
oraz montaż odpowiednio ukształtowanych arkuszy blachy do płaszczy-
zny obwodu drukowanego.
Najczęściej do wytworzenia klatek, ze względu na dobre właściwości
ekranujące, stosuje się blachę stalową, mosiężną, berylową lub miedzianą.
Właściwości te są skutkiem: po pierwsze, dobrej przewodności elektrycz-
nej, co skutecznie tłumi energię fal oraz po drugie, zjawiskiem niedopa-
sowania impedancji na granicy dwóch ośrodków tj. metalu i powietrza,
przez co występuje zjawisko odbicia. Grubość stosowanych blach zamyka
się w granicach do 2 mm, co zapewnia tłumienie na poziomie 100 dB.
Montaż ekranów często wykonuje się ręcznie, lutując je w odpowied-
nich miejscach do płaszczyzny masy obwodu drukowanego. Ostatnio po-
jawia się jednak tendencja do automatycznego montażu ekranów, gdzie
odpowiednie arkusze są układane jak inne elementy SMT. Sytuacja taka
jest jednak możliwa w przypadku ekranów o ograniczonej powierzchni,
ponieważ pojemność cieplna większych arkuszy uniemożliwia prawi-
dłowe ich przylutowanie w procesie automatycznym. Aby uniknąć tego
problemu, możliwe jest również zastosowanie odpowiedniego kleju prze-
wodzącego.
Inną metodą tak wykonania, jak i montażu ekranu, jest umieszczenie
w obrębie obwodu drukowanego odpowiednio ukształtowanych fartu-
74 ELEKTRONIKA PRAKTYCZNA 7/2009
NOTATNIK KONSTRUKTORA
R E K L A M A
chów, na które następnie nakładane są właści-
wie wypro?lowane arkusze zamykające ekran.
Metoda taka jest bardziej kosztowna, jednak
pozwala na zdecydowanie wygodniejsze serwi-
sowanie produktu.
Wybierając technologię montażu kon-
struktor może jednocześnie rozwiązać pro-
blem odpowiedniego odprowadzenia energii
cieplnej zgromadzonej wewnątrz ekranu.
Warto w tym celu stosować metodę polega-
jącą na nakładaniu na grzejące się elementy
termoprzewodzącej gąbki, na którą później
nałożony zostaje arkusz ekranu, pełniący
jednocześnie rolę radiatora (rys. 2).
Najważniejszym czynnikiem jaki kon-
struktor musi wziąć pod uwagę, jest prawi-
dłowe podłączenie ekranu do masy. Sytuacja
wydaje się prosta w przypadku, gdy mamy
do czynienia z ekranem umieszczonym tylko
po jednej stronie obwodu. W takim przypad-
ku możemy płaszczyznę masy znajdującą
się w warstwie wewnętrznej wyprowadzić
za pomocą standardowych przelotek zagrze-
banych do warstwy zewnętrznej, po czym
odpowiednio ukształtować w ścieżkę odpo-
wiadającą kształtowi nakładanego ekranu.
Tak ukształtowane połączenie musi mieć
zdjętą solder maskę, w miejsce której nale-
ży umieścić maskę pasty, bądź kleju (rys. 3),
co umożliwia szczelny montaż arkusza i za-
pobiegając przedostawaniu się szkodliwego
promieniowania.
Sytuacja nieco komplikuje się, gdy musi-
my ekrany umieścić po obu stronach płytki
obwodu. W takiej kon?guracji nie powinno
stosować się zwykłych przelotek (w zależno-
ści od maksymalnej częstotliwości jaką chce-
my ekranować), lecz zastosować tak zwane
mikroprzepusty. Należy to zrobić, ponieważ
fale elektromagnetyczne mogłyby swobodnie
przemieszczać się poprzez otwór przelotki na
drugą stronę płytki, wprowadzając zakłócenia
w pakiet elementów chroniony drugim ekra-
nem.
Otwory
Bardzo często w praktyce pojawia się
konieczność wykonania w ekranie otworów.
Ich rola sprowadza się do dwóch funkcji. Po
Rys. 2.
pierwsze, mają za zadanie kompensować
szkodliwe zjawiska powstające na skutek
nagrzewania się blachy w trakcie montażu,
bądź wzrostu temperatury komponentów
(zwłaszcza wtedy, gdy ekran pełni też funk-
cję radiatora). Po drugie, są one przerwami
w strukturze dla tak zwanej interakcji z użyt-
kownikiem, czyli - innymi słowy, są otwo-
rami wykonanymi pod wyświetlacze, złącza,
potencjometry, przyciski itp. Bez względu
na przyczynę stosowania istnieją pewne
uwarunkowania, które muszą być spełnio-
ne, aby zapewnić odpowiednią skuteczność
ekranowania. W sytuacji, gdy w strukturze
ma znajdować się pojedynczy otwór, aby nie
zmniejszać tłumienia ekranu, należy go od-
powiednio ukształtować w falowód (rys. 4).
Tak ukształtowany otwór, posiada swoją
częstotliwość graniczną, poniżej której bę-
75ELEKTRONIKA PRAKTYCZNA 7/2009
Projektowanie płytek
Rys. 3.
Rys. 4.
Rys. 5.
elementów i/lub układów ?ltrujących. Ważne
jest odpowiednie izolowanie arkusza ekranu
w miejscu, gdzie znajdują się takie elementy.
Sytuację taka dla ?ltru w postaci rezystora,
bądź dławika włączanego w szereg przedsta-
wia (rys. 5).
Aby uzyskać najlepsze efekty ważne jest,
aby ekran w miejscu ułożenia układu ?ltru
był podłączony do płaszczyzny odniesienia
(GND). W przeciwnym wypadku skuteczność
tłumienia ulegnie zmniejszeniu. Płaszczyzna
taka powinna być maksymalnie jednorodna,
najlepiej wypełniająca jedną warstwę elek-
tryczną zadeklarowaną w stosie warstw pro-
jektu.
W przypadkach, gdy z przyczyn ekono-
micznych możemy do budowy urządzenia
wykorzystać jedynie obwód dwuwarstwowy,
zalecane jest, aby komponenty umieszczać
wyłącznie z jednej strony płytki, natomiast
stronę drugą poświęcić na uzyskanie jak naj-
bardziej jednorodnej płaszczyzny masy. Jeże-
li taka sytuacja jest niemożliwa, czyli kompo-
nenty i połączenia muszą być rozmieszczone
z obu stron druku, to należy maksymalnie
wypełnić powierzchnią masy newralgiczne
rejony. Tylko taka metoda rozprowadzenia
masy zapewni wysoką skuteczność ?ltrowa-
nia.
W ekstremalnych przypadkach, gdy tra-
dycyjne metody ?ltracji nie zdają egzaminu,
należy sięgnąć po galwaniczną separację
w postaci optoizolatorów bądź transforma-
torów.
Przyszłość
Mimo iż opisane w artykule techniki
ekranowania są stosowane z powodzeniem,
to trwają badania nad ich udoskonaleniem.
Najbardziej dostrzegalną wadą współcze-
snych rozwiązań jest powstawanie odbić
zarówno składowej elektrycznej jak i magne-
tycznej fali. Trwają intensywne prace nad
materiałami z grupy tworzyw sztucznych
mogącymi pochłaniać energię fal, poprzez
rozproszenie jej w postaci ciepła. Materiały
takie już są stosowane w tak zwanych ko-
morach bezechowych, służących do badań
EMC.
inż. Tomasz Świontek
tomekfx@o2.pl
względu lepiej stosować (o ile to możliwe)
wiele otworów o małej średnicy rozłożonych
na pewnej powierzchni, niż jeden o dużych
gabarytach.
Filtrowanie
Jak już wcześniej wspomniałem, dla osią-
gnięcia wysokiej skuteczności ekranowania
konieczne jest zastosowanie odpowiednich
metod ?ltrowania. Filtrowanie jest koniecz-
ne, aby do pakietu chronionej powierzchni
obwodu nie dostały się zakłócenia propago-
wane przez połączenia kablowe ze środowi-
ska zewnętrznego. Najczęściej ?ltracja spro-
wadza się do prawidłowego rozmieszczenia
dzie zachowywał się jak tłumik. Częstotli-
wość ta w przypadku falowodu o przekroju
kołowym, zależy od średnicy D, i możemy ją
wyznaczyć ze wzoru:
f= (1,75×1010
)/D
Z praktycznego punktu widzenia ważna
jest średnica otworów, a nie ich liczba. Z tego
Zobacz więcej w kategorii Notatnik konstruktora