Wraz z rozwojem technologii, oświetlenie LED zyskuje coraz większą popularność. Diody LED dużej mocy (kilku- lub kilkunastowatowe) dla osiągnięcia optymalnych warunków pracy wymagają stosowania zasilaczy stałoprądowych, które nie są tak proste w konstrukcji i tak powszechne jak stałonapięciowe.
Ponadto duża moc skupiona w jednym punkcie wymusza konieczność stosowania specjalnych płytek drukowanych na podłożu aluminiowym pełniących rolę radiatorów, do których takie diody powinny być lutowane. Znacznie prostsze w stosowaniu są elastyczne taśmy z diodami LED zasilane stałym napięciem 12 V. Ich głównymi zaletami jest łatwość obsługi od strony elektrycznej, możliwość estetycznego ukrycia dzięki elastycznej i podłużnej formie oraz uzyskiwanie oświetlenia bez tak wyraźnej granicy cienia, jak w przypadku źródeł punktowych.
Aby taśma LED po prostu zaświeciła, potrzebujemy wyłącznie 12-woltowego zasilacza lub dowolnego innego źródła napięcia o tej wartości. Idąc dalej, zamiast po prostu włączać taśmę LED możemy ustawiać różne poziomy jej jasności lub dobierać kolor oświetlenia w zależności od nastroju. Wystarczy do tego odpowiedni sterownik i - dla uzyskania różnych barw światła - taśmy trójkolorowe z diodami LED RGB: czerwonymi, zielonymi i niebieskimi.
Oczywiście, już od dawna istnieją urządzenia sterujące taśmami LED jedno- i wielokolorowymi. Najczęściej są one kontrolowane z dołączonych pilotów na podczerwień lub czasem także radiowych. Jednak mało jest rozwiązań, w których można jednym pilotem sterować kilka różnych taśm. Podobnie jest z możliwością sterowania wielu pasków LED przy pomocy komputera lub własnego urządzenia nadrzędnego przez jakiś standardowy interfejs. Wreszcie funkcjonalność dostępnych rozwiązań, szczególnie tych zdalnie sterowanych, jest narzucona przez producenta i raczej nie będziemy mieć możliwości jej modyfikacji.
Proponowane rozwiązanie ma na celu ułatwienie konstruktorom uzyskanie urządzenia bardziej elastycznego niż te dostępne w handlu, jednak zachowując istotny parametr, jakim jest niewygórowana cena (choć i tak wyższa niż w przypadku importu z Chin). Ponadto, urządzenie było projektowane tak, aby dało się je zbudować z elementów łatwo dostępnych lub takich, dla których bez problemu da się znaleźć pełnowartościowe zamienniki.
Dzięki opisywanemu układowi można zarówno scentralizować jak i zdecentralizować sterowanie paskami LED: uzyskujemy możliwość ustawiania jasności bądź koloru każdego paska z dowolnego miejsca bez fizycznego przenoszenia pilota. Integracja sterownika z innymi urządzeniami domowymi i włącznikami ściennymi bądź zdalnymi także może stać się nieco prostsza niż w przypadku rozwiązań produkowanych masowo.
Dopisanie kodu podającego odpowiednie rozkazy do opisywanego sterownika (lub wielu sterowników) jest bowiem całkiem prostym zadaniem dla Czytelników mających choćby odrobinę doświadczenia z programowaniem interfejsu szeregowego w mikrokontrolerach lub na komputerze. Możemy wreszcie dowolnie modyfikować funkcjonalność sterownika taśm dysponując wyłącznie darmowymi narzędziami programowymi oraz niedrogim, ogólnodostępnym programatorem.
Sprzęt
Schemat blokowy sterownika przedstawiono na rysunku 1. Urządzenie zostało zaprojektowane w dwóch prawie identycznych (może lepsze słowo to "komplementarnych") wersjach. Centralnym elementem jest oczywiście mikrokontroler, tutaj STM32F103 (testy były przeprowadzane na modelu STM32F103RBT6).
Wybór mikrokontrolera był podyktowany jego popularnością, dobrym stosunkiem funkcjonalności do ceny, a przede wszystkim ilością dostępnych timerów z możliwością generowania sygnałów o modulowanej szerokości impulsów (PWM). Na rys. 1 zaznaczono, z których timerów (moduły TIM) korzystają poszczególne kanały wyjściowe OUT0...OUT9. Dodatkowo, w wersji firmware’u z protokołem Modbus potrzebny jest kolejny timer, tutaj TIM2, natomiast nie ma potrzeby używania go w wersji z protokołem SPPoB.
Mamy też dodatkowe wyjście zasilania na złączu CON4. Jeśli zaplanujemy stosowanie innych urządzeń z interfejsem RS-485, to przy okazji dołączania ich do magistrali warto będzie doprowadzić do nich zasilanie. Zasilanie taśm LED wymaga nieraz całkiem mocnego zasilacza, a w takiej sytuacji łatwo o pewien nadmiar wydajności prądowej. Z tego nadmiaru najczęściej bez problemu można uszczknąć kilka do kilkuset miliamperów do wygodnego zasilania klawiatur sterujących lub "inteligentnych" czujników automatycznie włączających oświetlenie.
Schemat ideowy sterownika taśm w wersji z kluczowanym napięciem +12 V przedstawiono na rysunku 2. Do kluczowania wykorzystuje on tranzystory z kanałem P. Alternatywnie można zbudować wersję z tranzystorami N, w której kluczowana jest masa, a napięcie +12 V doprowadzone jest na stałe. Obie wersje różnią się jedynie fragmentem schematu przedstawionym na rysunku 3. Inne są oczywiście tranzystory mocy oraz podłączenie sygnałów do "driverów" ich bramek.
Do budowy prototypu w wersji P-MOS zastosowano tranzystory AP4435GJ-HF- 3TB w obudowach TO-251, natomiast dla wersji N-MOS były to AP9962GJ-HF-3TB w takiej samej obudowie. Tranzystory te charakteryzują się niezłymi parametrami elektrycznymi przy niskiej cenie.
W przypadku trudności ze zdobyciem wyżej wspomnianych tranzystorów, można śmiało rozważyć zastosowanie zamienników, ponieważ układ sterownika jest mało wrażliwy na ich parametry. Chyba jedynym mniej typowym parametrem zastosowanych tranzystorów jest relatywnie niskie napięcie progowe VGS(th) mieszczące się w przedziale od 1 do 3 V przy sporym maksymalnym prądzie drenu wynoszącym 20 A dla P-MOS i 32 A dla N-MOS (o niskie napięcie VGS(th) łatwiej wśród tranzystorów FET przeznaczonych do małych prądów).
Jeśli popatrzeć na rozwiązanie driverów dla bramek tranzystorów mocy, to może się wydawać, że jest to rozwiązanie co najmniej wątpliwe - bramki są bowiem sterowane przez komparatory zbudowane z jednych z najtańszych i najpopularniejszych wzmacniaczy operacyjnych LM324. Zastosowanie rozwiązania z komparatorami ma jednak kilka zalet.
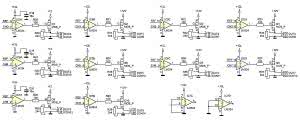
Rysunek 3. Schemat ideowy bloku wyjściowego sterownika taśm LED w wersji z tranzystorami N-MOS. Główna część schematu jest identyczna jak na rysunku 2
Przede wszystkim nie podwyższa kosztów urządzenia, ponieważ ceny dedykowanych układów driverów są zbliżone do ceny zastosowanych tranzystorów, co przy skali 10 kanałów i kilku sterowników zaczyna generować odczuwalną różnicę.
W razie braku wybranego układu drivera trudniej jest znaleźć dla niego pasujący na płytkę zamiennik, podczas gdy zastosowane wzmacniacze operacyjne można nabyć w przysłowiowym sklepie za rogiem. Można było także zaprojektować drugi układ z komplementarnymi tranzystorami działający z identycznym oprogramowaniem (bez konieczności odwracania przebiegów PWM z mikrokontrolera) przez prostą zamianę wejść komparatorów.
Przy zastosowanym prostym układzie sterowania bramek tranzystorów oraz częstotliwości przebiegu PWM wynoszącej 550 Hz, tranzystory nie wydzielają zauważalnych ilości ciepła, nawet pod obciążeniem ok. 5 A. Na rysunku 4 przedstawiono zrzuty ekranu oscyloskopu dla włączania i wyłączania obciążenia w wersji N-MOS.
W kanale pierwszym (górny wykres) widzimy napięcie na bramce tranzystora, natomiast w drugim, napięcie na obciążeniu (tutaj prąd po załączeniu to ok. 2 A). Czas narastania napięcia na bramce można szacować na ok. 10 µs, jednak dzięki niskiemu napięciu załączenia VGS(th) tranzystory włączają obciążenie znacznie szybciej, tj. w czasie niewiele przekraczającym 1 µs.
Sumaryczna obciążalność sterownika podyktowana jest głównie ograniczeniami jego płytki drukowanej i zastosowanego złącza zasilania CON3. W egzemplarzach prototypowych zastosowano główne złącze zasilania o maksymalnym prądzie 24 A. Kolejnym ograniczeniem jest maksymalny prąd, który mogą przewodzić obwody drukowane na płytce sterownika - przy dużym obciążeniu ścieżki będą się nagrzewać.
Zasilanie i zabezpieczenia
Blok zasilania sterownika taśm LED składa się z dwóch popularnych stabilizatorów i układów zabezpieczających. Napięcie ok. 5 V uzyskuje się z układu IC2 (L5972D). Układ ten właściwie pełni funkcję stabilizatora wstępnego, z którego dalej napięcie jest obniżone do 3,3 V w układzie IC3 (LM1117-3.3). Przy okazji napięcie 5 V wykorzystywane jest do zasilania transceivera RS-485.
Dzięki zastosowaniu wstępnej stabilizacji na dobrym stabilizatorze impulsowym, nie ma problemu z wydzielaniem dużej ilości energii w postaci ciepła, czego następstwem jest to, że sam sterownik pobiera mało prądu (poniżej 30 mA). Może to mieć znaczenie ekonomiczne, jeśli sterownik taśm ma być cały czas podłączony do zasilania.
Układy zabezpieczeń mogą uratować sterownik i paski LED w razie wystąpienia przypadkowych przepięć lub bardziej pechowej awarii zasilacza. Jednak nie są one konieczne do działania sterownika i można ich albo nie montować (w przypadku diod TVS i warystora), albo zastąpić zworami (bezpieczniki polimerowe).
Warystor może być przydatny np. wtedy, gdy planujemy stosować długie przewody pomiędzy zasilaczem a sterownikiem lub "niepewny" zasilacz. Gdy zasilacz znajduje się blisko urządzenia, można śmiało zrezygnować z warystora. Z racji, że warystor może wydzielać dużo energii w momencie wystąpienia przepięcia, zalecane jest zabezpieczenie całego układu dodatkowo zewnętrznym, szybkim bezpiecznikiem włączonym na linii +12 V pomiędzy sterownikiem a zasilaczem.
W przeciwnym wypadku nadmiar energii może spowodować dosłowne spalenie warystora, co w czarniejszym scenariuszu może wywołać poważne niebezpieczeństwo pożaru. Zarówno bezpiecznik jak i warystor należy dobrać w zależności od planowanego maksymalnego prądu zasilania. Napięcie pracy warystora powinno być o co najmniej kilka woltów wyższe niż 12 V, aby nie wywoływać "fałszywych alarmów", które przyczyniają się do degradacji parametrów warystora.
Tak czy inaczej, najbardziej wrażliwe elementy sterownika zostały zabezpieczone dodatkowo diodą D1. Jako D1 w egzemplarzach testowych zostały zastosowane jednokierunkowe diody TVS o napięciu znamionowym ok. 18 V, model SMBJ18A. Bezpiecznik polimerowy F1 pomaga uchronić diodę D1 przed przegrzaniem w przypadku podawania zbyt wysokiego napięcia na wejście zasilania przez dłuższy czas.
Komparatory pracujące jako drivery tranzystorów mocy nie mają własnego lokalnego stabilizatora, dlatego zasilane są przez koralik ferrytowy L1, tłumiący zakłócenia o wyższych częstotliwościach, oraz dodatkowo ich zasilanie jest filtrowane przez kondensatory C18-C20.
Te elementy warto zastosować, ponieważ na szynie zasilania +12 V mogą pojawić się zakłócenia wynikające z impulsowego charakteru obciążenia. Wyjście zasilania (na złączu CON4) dla innych urządzeń z interfejsem RS-485 także jest w pewnym stopniu zabezpieczone. Przed skutkami zewnętrznego zwarcia chroni je polimerowy bezpiecznik F2, natomiast dioda TVS D5 ma częściowo chronić sterownik przed przepięciami przenikającymi z wyjścia zasilania.
Przewidziano także miejsce na diody TVS (D3 i D4) dla linii A i B interfejsu RS-485. Diody D3 i D4 nie muszą być specjalizowane dla RS-485 - płytka została zaprojektowana pod popularne obudowy większych diod, DO-214AA. W wykazie elementów uwzględniono diody TVS jednokierunkowe na 12 V (zakładamy, że wszystkie urządzenia będą na wspólnej masie). Z racji jednak, że transceivery RS-485 mogą pracować także w zakresie napięć ujemnych na magistrali, można tutaj zastosować diody dwukierunkowe na nieco niższe napięcie.
Interfejsy zewnętrzne
Interfejs RS-485 zrealizowany jest standardowo. Z racji, że do zasilania transceivera IC4 przewidziano napięcie 5 V ze stabilizatora o sporej wydajności, można zastosować zarówno leciwy i prądożerny SN75176B, jak też jego nowocześniejsze odpowiedniki, np. MAX485. Wejście USART2_RX (wyprowadzenie PA3) mikrokontrolera wg dokumentacji producenta nie akceptuje napięcia 5 V, dlatego potrzebny jest co najmniej szeregowy rezystor R14 na wyjściu odbiornika (nóżka 1) w układzie IC4.
Wartość 470 Ω dla R14 będzie wystarczająca dla ograniczenia prądu wstrzykiwanego do mikrokontrolera w stanie wysokim (producent zaleca, by prąd ten nie przekraczał 5 mA). Właściwe ograniczenie napięcia następuje w mikrokontrolerze, na wewnętrznych elementach zabezpieczających jego wejścia.
W sterowniku taśm możliwe jest zarówno zamontowanie terminatora (R18) jak i rezystorów fail-safe (R17, R19) dla magistrali RS-485. Wg zasad, terminatory stosujemy na końcach magistrali. Rezystory fail-safe wystarczy umieścić w jednym miejscu magistrali (np. razem z jednym terminatorem). W praktyce przy krótkich magistralach i niskich szybkościach transmisji terminatory mogą nie być potrzebne, natomiast przydatne są rezystory fail-safe, które mogą mieć wartości nawet rzędu kilku kiloomów jeśli nie stosujemy terminatorów.
Jedynymi elementami sterownika przewidzianymi do bezpośredniej interakcji z użytkownikiem (tutaj właściwie serwisantem) są przełączniki typu "dipswitch" SW1 i SW2 oraz diody LED1 i LED2. Dodatkowa dioda LED3 służy do wskazywania obecności napięcia zasilania. Przełączniki SW1 i SW2 są bardzo przydatne do ustawiania adresu urządzenia zarówno w wersji dla protokołu Modbus jak i SPPoB. Trzeba tylko brać pod uwagę, że nie każde ich ustawienie jest poprawne bądź ma sens, np. 0000 0000 dla Modbus czy 1111 1111 dla SPPoB.
Montaż
Płytka drukowana sterownika taśm LED została zaprojektowana tak, aby dało się ją umieścić w obudowie typu Z-101 z możliwością montażu na szynie DIN. Schemat montażowy wersji N-MOS jak i P-MOS przedstawiono na rysunku 5.
Jeśli planujemy umieszczenie płytki w obudowie Z-101, należy wyciąć dwa narożniki z prawej strony płytki wg linii zaznaczonych na warstwie opisowej (najlepiej jest to zrobić jeszcze przed rozpoczęciem montażu elementów elektronicznych). Konieczność samodzielnego wycinania narożników podyktowana jest tym, że wykonanie płytek o nietypowych kształtach bywa droższe niż prostokątnych.
Z racji dużej dopuszczalnej obciążalności poszczególnych kanałów, całe urządzenie może pobierać znaczny prąd. Z tego powodu na płytkach w obu wersjach złącze śrubowe głównego zasilania CON3 jest nieco odsunięte od złącza sąsiedniego CON4, by dało się zastosować większe gabarytowo złącze o dużym maksymalnym prądzie przewodzenia, np. 24 A jak na fotografii 1. Dodatkowo, ścieżki na płytkach drukowanych, które mają przewodzić największy prąd, mają częściowo odsłoniętą warstwę maski lutowniczej, aby można było np. pokryć je grubszą warstwą spoiwa lub nawet wlutować dodatkowy drut zmniejszający ich rezystancję.
Sam montaż elementów raczej nie wymaga dodatkowego komentarza. W wersji okrojonej z zabezpieczeń można pominąć montaż diod TVS i warystora, a zamiast bezpieczników polimerowych zamontować zwory. Zworę można wmontować także zamiast koralika ferrytowego L1. Więcej szczegółów na temat doboru elementów zabezpieczających znajdziemy w sekcji Zasilanie i zabezpieczenia niniejszego artykułu.
Przed wlutowaniem mikrokontrolera, warto sprawdzić poprawność działania stabilizatorów dostarczających napięcia zasilające +5 V oraz +3,3 V. Napięcie +5 V może być w rzeczywistości nieznacznie niższe z racji, że rezystory R8 i R10 użyte do sprzężenia zwrotnego dobrane są spośród popularnych wartości (nie ma to jednak negatywnego wpływu na pracę układu). Jeśli jednak ktoś chciałby uzyskać dokładniejszy poziom tego napięcia, należy dobrać inne wartości rezystorów R8, R9 i R10 ustalających napięcie wyjściowe IC2.
Po zamontowaniu wszystkich elementów i sprawdzeniu poprawności montażu można zaprogramować mikrokontroler dostarczonym kodem wynikowym, ewentualnie wcześniej samemu skompilować źródła. Do zaprogramowania będzie potrzebny programator z interfejsem SWD, zgodny z ST-Link. Jako programatora można również użyć którejś z płytek z rodziny "Discovery", wyprowadzając interfejs SWD z ich wbudowanego programatora.
W przypadku stosowania programatora ST-Link lub zamiennika, należy zapewnić mu napięcie 3,3 V na jego złączu, choć nie jest ono wystawione na CON2 sterownika taśm. W przypadku programatora ZL30PRGv2 wystarczy zewrzeć jego wyprowadzenia o numerach 1 i 19 na głównym złączu JTAG/SWD. Po poprawnym zaprogramowaniu w obu wersjach sterownika powinna migać dioda LED1.
Programy sterujące
Programy dla obu wersji zostały napisane w języku C, a dołączone projekty były kompilowane za pomocą kompilatora GCC z pakietu Yagarto. Domyślnie powinny działać polecenia make all (kompilacja) i make clean (usuwanie plików wynikowych z katalogu projektu).
Programy sterujące nie korzystają z żadnego systemu operacyjnego, a główna pętla programowa znajduje się w plikach main.c, w funkcjach main. Stamtąd jest wywoływana m.in. funkcja ledTask, odpowiedzialna za wpisywanie zadanych z zewnątrz poziomów jasności do poszczególnych kanałów z zapewnieniem ewentualnego płynnego przejścia od jasności aktualnej do zadanej. Funkcja ledTask jest prawie identyczna dla wersji z interfejsem Modbus jak i SPPoB - różnice dotyczą głównie organizacji struktur danych, natomiast jej ogólna logika działania jest taka sama.
Sterowniki generatorów PWM wbudowanych w mikrokontroler znajdziemy w drivers/pwm.c (takie same dla obu wersji). Moduł pwm.c ma bardzo prosty interfejs składający się z dwóch funkcji widzianych na zewnątrz: pwmInit oraz pwmSet. W funkcji pwmInit konfigurowane są odpowiednie sygnały zegarowe, wszystkie moduły TIM, ich wyjścia OC (Output Compare) oraz aktywowane są alternatywne funkcje odpowiednich wyprowadzeń GPIO.
Po przeprowadzeniu inicjalizacji można wywoływać funkcję pwmSet o następującej deklaracji: void pwmSet(uint8_t channel, uint8_t value);. Funkcja przyjmuje dwa dość oczywiste parametry. Pierwszy (channel) mówi, do którego kanału w sterowniku chcemy wpisać wartość, natomiast samą wartość jasności przekazujemy w drugim argumencie, value. Poprawnie obsługiwany zakres argumentu channel to liczby całkowite w zakresie od 0 do 9 odpowiadające kanałom wyjściowym sterownika. W parametrze value można przekazywać liczby od 0 do 255.
Liczba zadawanych poziomów jasności jest co prawda 8-bitowa, jednak wyjściowe kanały pracują z rozdzielczością 16-bitową. Przekształcenie liczby wejściowej na wysterowanie kanału realizowane jest przy pomocy funkcji kompensującej nieliniowy charakter postrzegania jasności przez ludzki wzrok.
Przekształcanie wejściowych liczb 8-bitowych z argumentu value na liczby 16-bitowe odbywa poprzez 256-elementową tablicę stałych wartości 16-bitowych o nazwie PWM_LUT (definicja w pliku pwm_lut.h w katalogach głównych projektów). Liczba value będąca argumentem funkcji pwmSet używana jest jako indeks tej tablicy.
Co prawda moc obliczeniowa i częstotliwość taktowania mikrokontrolera pozwoliłyby na przeprowadzenie nawet dość złożonych obliczeń na bieżąco, to jednak rozwiązanie z tablicą LUT (od lookup table) powoduje, że czas przekształcania value na współczynnik wypełnienia jest taki sam niezależnie od stopnia złożoności funkcji korekcji, a dodatkowo możemy sobie pozwolić na większą swobodę w doborze samej funkcji.
Krzywa korekcji
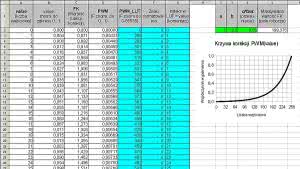
Rysunek 6. Nagłówek arkusza pwm_lut.ods służącego do generowania krzywych korekcji współczynnika wypełnienia wyjściowych przebiegów PWM
Wzrok i słuch ludzki działają - można by rzec - "w skalach logarytmicznych". Gdy jest bardzo ciemno, oczy są czułe na najmniejsze zmiany natężenia światła, a kiedy jest cicho, słyszymy najdrobniejsze szmery. Natomiast przy bardzo dużych natężeniach światła lub dźwięku, zauważalne zmiany występują dopiero po wyraźnym zwiększeniu mocy źródła czy to dźwięku, czy światła.
Gdyby zatem sterować jasnością diod LED w paskach liniowo, to wydawałoby nam się, że daleko przed połową skali diody mają już pełną jasność, więc jeśli założymy, że postrzeganie ma charakter logarytmiczny, to jego kompensacja może być przeprowadzona przez działanie odwrotne, czyli przez zastosowanie funkcji wykładniczej. Takie przekształcenie może zostać zrealizowane w tablicy PWM_LUT sterownika taśm LED.
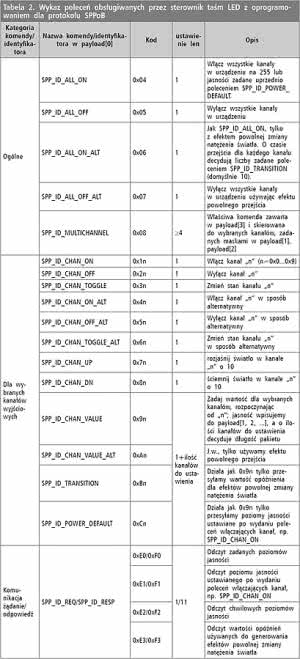
Tabela 2. Wykaz poleceń obsługiwanych przez sterownik taśm LED z oprogramowaniem dla protokołu SPPoB
Liczby wyjściowe w tablicy PWM_LUT oczywiście nie muszą być dobierane i wpisywane ręcznie każda z osobna. Może je za nas wygenerować prosty arkusz kalkulacyjny, z którego tylko skopiujemy wyniki. Taki arkusz z przykładową krzywą korekcji został dołączony do materiałów do niniejszego artykułu i znajduje się w pliku pwm_lut.ods. Z pewnością może on ułatwić dopasowanie funkcji korekcji jasności do posiadanych pasków LED lub po prostu wedle własnego uznania.
Jest on opracowany w programie Calc z pakietu LibreOffice, aby dało się bez trudu i za darmo uzyskać możliwość jego otwarcia i edycji dla wielu systemów operacyjnych. Zrzut nagłówka i kilku początkowych wierszy tego arkusza przedstawiono na rysunku 6. Kolejne liczby wejściowe (te, które będziemy zadawać w argumencie value) znajdują się w kolumnie A.
Dla ułatwienia liczby te są znormalizowane do zakresu od 0 do 1 (kolumna B) i dopiero w takiej postaci poddawane są przekształceniu przez funkcję korekcji. Dla niezerowych indeksów value funkcja korekcji FK zadana jest następującą zależnością FK = a·(10b·value - 1) + offset, natomiast dla indeksu value wynoszącego 0 ma ona wartość 0.
Parametr a w funkcji FK możemy zadawać w komórce I2 dostarczonego arkusza i może on być używany opcjonalnie do pionowego skalowania krzywej (jeśli nie jest potrzebny, ustawiamy go na 1). Natomiast parametr b zadawany w komórce J2 decyduje o tym, jak mocno "zagięta" jest funkcja FK (wystarczy wykonać parę prób na arkuszu, aby zobaczyć o co chodzi).
Dodatkowy parametr offset zadawany w K2 służy do zapobiegania pustym wartościom na początku skali. Bez niego początek skali zawierałby liczby generujące tak krótkie impulsy, że nie pojawiałyby się one na wyjściach sterownika. Odpowiednio dobrany (choćby eksperymentalnie) parametr offset spowoduje, że każda niezerowa liczba w value spowoduje jakieś wysterowanie diod LED w paskach.
Pojawiająca się w komórce L2 maksymalna wartość FK osiągana w kolumnie C pozwala znormalizować wyjściową wartość funkcji FK do zakresu 0...1, a dalej na liczbę 16-bitową z zakresu 0...65535. Wyróżnioną na kolor jasnoniebieski zawartość kolumn E, F i G wystarczy zaznaczyć, skopiować i wkleić do wnętrza tablicy PWM_LUT w pliku pwm_lut.h. Oczywiście właściwe wartości są w kolumnie E, natomiast reszta (F i G) to przecinki wymagane przez składnię języka C i nieobowiązkowe komentarze zawierające numer indeksu w tablicy PWM_LUT dla każdej wartości.
W indywidualnym doborze preferowanej funkcji korekcji pomocne może być zaobserwowanie trwającego ok. 3...4 sekundy, płynnego przejścia przez wszystkie wartości jasności (liniowa zmiana value od 255 do 0) i ocenienie subiektywnego wrażenia "liniowości" zmian.
Nie powinno się tej funkcji dobierać na podstawie bezpośredniej, bliskiej obserwacji diod LED w pasku, ponieważ jasne punktowe źródła światła mogą wywoływać chwilowe oślepienie. Lepiej będzie przykryć testową tasiemkę LED zwykłą, białą kartką papieru dla uzyskania światła rozproszonego i w ten sposób obserwować przejścia jasności.
Interfejs zewnętrzny - protokół Modbus
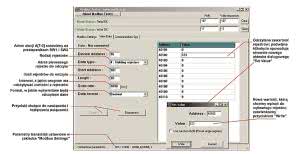
Rysunek 7. Widok okna programu Modbus Tester z wprowadzonymi ustawieniami do testowania zapisu i odczytu rejestrów sterownika
Wersja oprogramowania komunikująca się przez interfejs Modbus korzysta z popularnej i łatwiej w obsłudze biblioteki FreeModbus dostępnej na stronie http://goo.gl/JGDrtE. Przy domyślnych ustawieniach programu korzystamy z Modbus RTU, czyli binarnej odmiany protokołu. Parametry transmisji są następujące: 19200 baud, 8 bitów danych, 1 bit stopu, brak bitu parzystości.
Adres urządzenia (stacji) Modbus ustawiamy na przełącznikach SW1 i SW2 w zakresie od 1 do 247. Mapę rejestrów wewnętrznych sterownika taśm w wersji z protokołem Modbus przedstawiono w tabeli 1. Dla uproszczenia wszystkie zastosowane rejestry są typu holding register. Mamy zarówno możliwość wpisu wartości do poszczególnych rejestrów, jak i ich odczytu. Rejestry mają rozmiar 16 bitów, jednak wpisy do nich są ograniczone do liczby 255. Wpisanie większej liczby spowoduje jej automatyczną redukcję do 255.
Jasności dla poszczególnych kanałów wpisujemy do "rejestrów jasności" pod adresami 101 do 110, natomiast czas przejścia pomiędzy jasnościami jest zależny od liczb wpisanych do "rejestrów opóźnienia" w przestrzeni adresów od 201 do 210. Rejestrom jasności odpowiada w programie głównym tablica reg_powerSet, natomiast rejestry opóźnienia reprezentowane są tablicą reg_delay.
Każdy rejestr opóźnienia mówi ile (mniej-więcej) w milisekundach będzie trwała zmiana jasności kanału o 1. Wpisanie nowej (innej niż poprzednia) liczby do rejestrów jasności spowoduje stopniowe przejście do tej jasności po jednym kroku wykonywanym z opóźnieniem zadanym w odpowiednim rejestrze opóźnienia. Np. w rejestrze jasności wybranego kanału mamy liczbę 100, a wpisujemy 150.
W rejestrze opóźnienia dla tego kanału mamy liczbę 10, co odpowiada opóźnieniu ok. 10 ms na krok. Jasność zmieni się o: 150 - 100 = 50 jednostek, a przejście do nowej wartości będzie trwało 50·10 ms = 500 ms. Czas jednego kroku jest zadany stałym opóźnieniem w pętli głównej i efektywny czas opóźnienia jest zależny także od wykonania innych fragmentów kodu, stąd wspomnianą "ilość milisekund" należy przyjąć raczej jako wartość orientacyjną. Można oczywiście uzyskać bardziej precyzyjne odmierzanie czasu stosując inny mechanizm opóźnienia bazowego niż zastosowana, prosta funkcja delay_ms o stałym opóźnieniu.
Do przeprowadzenia wstępnych testów działania sterownika w wersji z interfejsem Modbus można użyć dowolnego programu obsługującego protokół Modbus od strony urządzenia nadrzędnego. Przykładem funkcjonalnego, prostego w obsłudze i darmowego programu jest Modbus Tester dostępny pod adresem http://goo.gl/TceCE5. Na rysunku 7 przedstawiono widok okna tego programu z objaśnieniami oraz ustawionymi parametrami do odczytu rejestrów jasności wraz z aktywnym okienkiem wpisu do rejestru o adresie 102.
Wykaz elementówRezystory: Kondensatory: Półprzewodniki: Inne: |
Interfejs zewnętrzny - protokół SPPoB
Wersja programu dla sterownika taśm LED z eksperymentalnym protokołem SPPoB ma rdzeń funkcjonalności bardzo zbliżony do wersji z protokołem Modbus, lecz ma nieco więcej opcji modyfikacji stanu wybranych kanałów. Po ogólny opis protokołu SPPoB odsyłam Czytelników do EP nr 10/2014, natomiast tutaj skoncentrujemy się na konkretnych przykładach.
Zestaw obsługiwanych komend przedstawiono w tabeli 2. Parametry transmisji są takie same jak dla interfejsu Modbus, tj. 19200 baud, 8 bitów danych, 1 bit stopu, brak bitu parzystości. Mechanizm działania przejść pomiędzy jasnościami (zaimplementowany w ledTask) działa także podobnie w obu wersjach.
Do testów warto skompilować źródła z makrodefinicją SPP_IGNORE_CRC ustawioną na "1" (plik spp_cfg.h w katalogu głównym projektu) i tak przygotowany plik binarny wgrać do pamięci Flash mikrokontrolera. Dzięki temu będziemy mogli wysyłać pakiety w formie makr z programu terminalowego terminalbpp ze strony http://goo.gl/qnzBbj i zamiast sumy kontrolnej na końcach pakietów wpiszemy dowolny bajt (w dalszych przykładach 0x00), a pakiet i tak zostanie przyjęty.
Zacznijmy od prostego ustawienia wartości w jednym kanale. Na rysunku 8 przedstawiono strukturę pakietu, w którym ustawiamy jasność kanału nr 3 na wartość 0x33 przy pomocy polecenia SPP_ID_CHAN_ VALUE (definicja w pliku spp_cmdid.h). Załóżmy teraz, że pakiet wysyła urządzenie o adresie 0xA0, a sterownik pasków LED ma adres 0xB0.
Wysyłany pakiet będzie zawierał ciąg liczb: [7E, B0, A0, 02, 93, 33, CRC]. Aby go wysłać, w programie terminalowym w polu wysyłania można wpisać ciąg znaków $7E$B0$A0$02$93$33$00. Zamiast sumy kontrolnej wysyłamy tutaj liczbę 0x00, natomiast znak "$" w programie terminalbpp (lub Terminal by Br@ y++) używany jest jako przedrostek liczby w formacie szesnastkowym.
Jeśli za pomocą tego samego polecenia SPP_ID_CHAN_VALUE zechcemy ustawić jasności w kanałach 3, 4 i 5 na odpowiednio 0x33, 0x44 i 0x55, to należy wysłać taki pakiet, jak na rysunku 9. Tak będą działały polecenia z tabeli 2 o kodach od 0x90 do 0xC0, dla których występuje parametr określający wartość nastawy.
Nieco prostsze będą polecenia jednobajtowe, służące do sterowania pojedynczych kanałów, o kodach 0x1n do 0x8n oraz ogólne: 0x04 do 0x07. Przykład pakietu włączającego domyślny poziom jasności w kanale 5 będzie następujący (adresy i zapis jak w poprzednim przykładzie): [7E, B0, A0, 01, 15, CRC].
Stosując komendę Multichannel możemy w jednym pakiecie wysłać jednakowe polecenie do wielu kanałów, np. wyłączyć wybrane kanały lub zadać im jednakowe poziomy jasności. Składnia pakietu Multichannel została omówiona w pierwszej części artykułu o protokole SPPoB. Tutaj przedstawię jedynie prosty przykład. W przypadku omawianego sterownika, gdy chcemy przy pomocy polecenia SPP_ID_CHAN_TOGGLE_ALT (0x60) odwrócić stany w kanałach 9, 8, 7, 5, 2, 0 (ich maska bitowa to 0000 0011 1010 0101 czyli 0x03A5), to wyślemy np. następujący pakiet: [7E, B0, A0, 04, 08, 03, A5, 60, CRC].
I wreszcie możemy odczytać aktualne ustawienia dla sterownika wysyłając żądania z odpowiednimi parametrami. Przykład sekwencji żądanie-odpowiedź z parametrem 0 oznaczającym odczyt zadanych jasności został przedstawiony na rysunku 10.
Podsumowanie i dalsze pomysły
Z racji dostępności kodów źródłowych i oczywiście schematów sprzętu, sterownik pasków LED można bez trudu dostosować do realizacji własnego pomysłu: zarówno w dziedzinie nowych efektów, jak i interfejsu zewnętrznego. Ponadto płytka drukowana jest kompatybilna z wieloma mikrokontrolerami STM32F103, również takimi, które mają duże ilości wewnętrznych pamięci.
Może to ułatwić zaszycie wewnątrz sterownika nawet całkiem rozbudowanej logiki działania. Wyprowadzony na zewnątrz interfejs RS-485 jest także bardzo uniwersalny i tani w implementacji. Dlatego nie powinno być trudności z wykonaniem przejściówek z innych interfejsów (USB, RS-232) lub wykonaniem zewnętrznych kontrolerów generujących polecenia Modbus lub SPPoB na podstawie danych odebranych np. z pilotów RC-5 czy modułów Bluetooth. Po modyfikacji oprogramowania urządzenie powinno nadawać się także do pracy jako generator "atmosfery" (ambient light) wokół monitora lub telewizora.
Robert Brzoza-Woch
robert.brzoza@gmail.com